The History of Bullet and Blast Proofing Personnel
From plate to polymer to nanoparticle, personal body armour has come a long way.
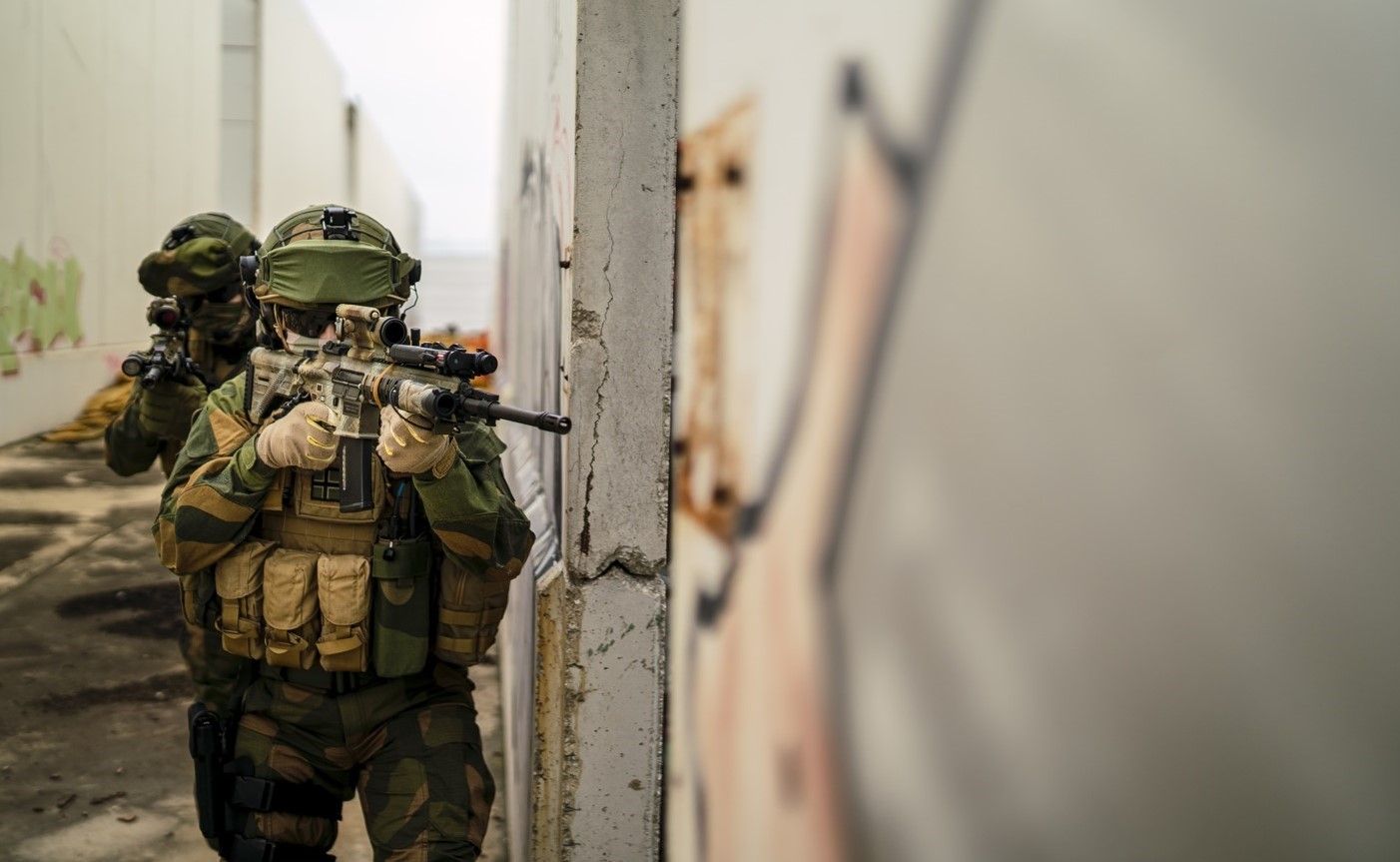
Protecting people from bullets and blasts is an evolving subject throughout history. From the chain mail of medieval knights to modern-day advanced nanoparticle-enhanced ceramic inserts, bullet and blast-proof technology is constantly improving.
The earliest recorded use of a bulletproof vest was in 1538 when the Duke of Bourbon was shot with a musket during the Battle of Pavia. His newly designed, anti-projectile armour served him well and he survived with only minor injuries.
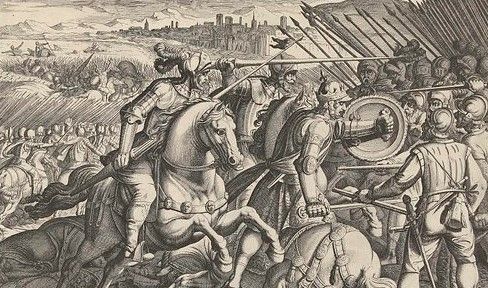
But it wasn't until the 1800s that the concept of a vest made of soft, flexible materials was developed using layers of silk to absorb impacts. It was relatively ineffective against bullets but could protect against shrapnel and other small fragments.
In 1897, Casimir Zeglen, a Polish priest and innovator, made a living conducting live presentations of his bulletproof coat at the Koster & Bial Music Hall stage in Manhattan. During the demonstration, Zeglen allowed himself to be shot by a .41 Colt revolver while wearing the coat which had several layers of tightly woven silk meshed together to intercept the bullet. Zeglen stated that he barely felt a tap but was certainly lying as there is more to anti-ballistics technology than stopping the penetrating force of a projectile.
Even today, soft body armour is limited by force dispersion as the impact force of a bullet is transmitted through a body even if the projectile is stopped. This pressure punch can result in severe bruising or damage to internal organs. Additionally, the silk armour Zeglen wore only offered protection from low-powered ammunition, making it incapable of stopping the more powerful 9mm Parabellum rounds introduced by Georg Luger in 1901.
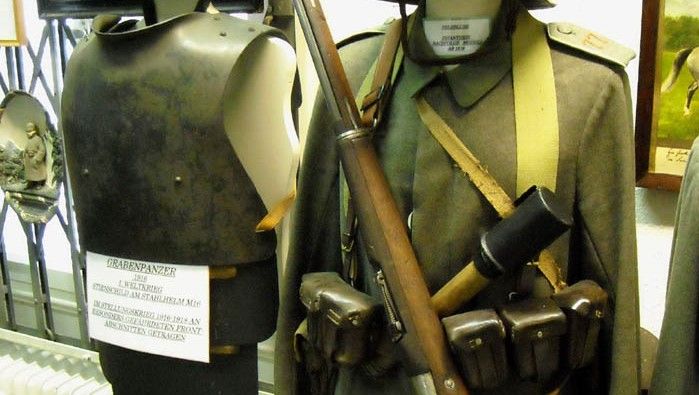
At the beginning of World War I, soldiers were sent to fight without any form of body armour. While advertisements from private companies showed that expensive body protection suits such as the Birmingham Chemico Body Shield was available, the average soldier could not afford them.
It was not until 1915 that official attempts were made by the British Army Design Committee to commission body armour, such as the 'Bomber's Shield' for bomber pilots who were poorly protected from anti-aircraft bullets and fragmentation. Or the Experimental Ordnance Board’s ‘necklet’ which was made of interwoven layers of silk and cotton which was stiffened with resin and able to stop bullets traveling at 600 feet per second.
As the war progressed, the British army medical services estimated that three-quarters of all battle injuries could have been prevented if effective armour had been issued.
Researchers began to seek out a synthetic alternative as natural materials lacked the necessary strength for more modern firepower.
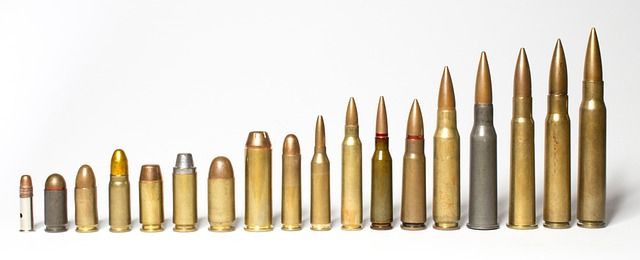
This led to a new type of bulletproof material emerging during the 1920s and 1930s, made from woven nylon layers criss-crossed over each other to create a flexible and durable protection vest. They were used primarily by law enforcement officers, particularly during the prohibition era.
This design was revised with a high-strength version of Nylon being used during the Korean War. However, it proved to be unpopular with soldiers who did not want to wear a bulky, heavy, and hot vest which provided only limited protection.
It wasn’t until the development of Aramid fibre, a chemical compound consisting of rigid polymer chains linked by strong hydrogen bonds that enable efficient mechanical stress transfer, that truly strong yet flexible material for bulletproofing became available.
In 1965, Stephanie Kwolek, a DuPont employee, found that while synthesizing new aromatic polyamides under certain conditions rod-like molecules lined up in parallel to create liquid crystals. By spinning the solution along this direction, a fibre with extraordinary strength was born. It was called Kevlar.
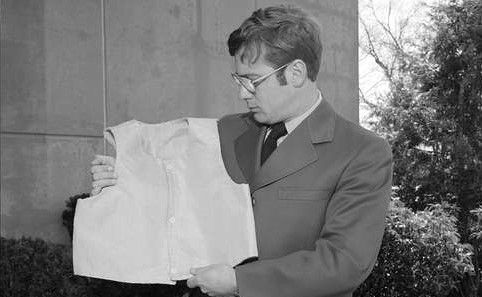
The modern-day bulletproof vest was developed during the 1970s by Richard A. Davis, a U.S. Marine, who was the first to use Kevlar in this role. The padding used was lighter and more flexible than previous vests, yet it offered superior protection. He was awarded Patent #3,971,072 for his innovation in 1975; the first vest that could stop a bullet fired from an automatic weapon.
In addition to woven Kevlar, other fibres and construction techniques have been developed for bulletproof fabric since the 1970s. These include DSM's Dyneema, Honeywell's Gold Flex and Spectra, Teijin Aramid's Twaron, Pinnacle Armor's Dragon Skin, and Toyobo's Zylon.
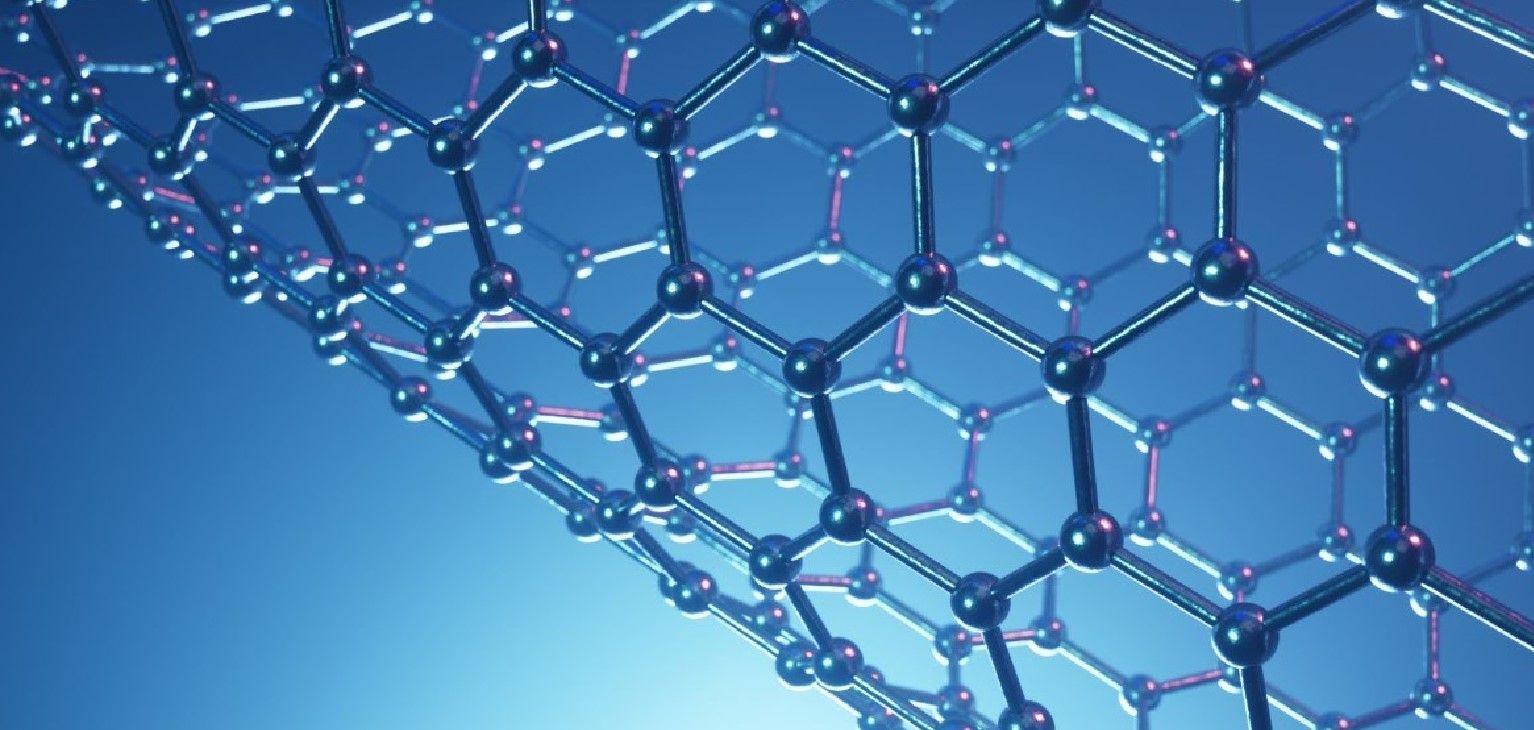
Today, most research into personal body armour is based on nanomaterials. This has resulted in considerable safety advances, including the development of DuPont’s exo-bulletproof material. Made from a composite of Kevlar, carbon nanotubes, and polymer fibres, DuPont claim that it is ten times stronger than steel yet flexible enough to be moulded to fit any shape.
Other products in the latest generation of protection technology are also based on nanomaterials, such as carbon nanotubes, embedded in a polymer matrix. This forms a material with high impact strength, low weight, and good flexibility. Layers of this substance are designed to stop bullets from a variety of firearms, including armour-piercing rounds. They are also blast-proof, withstanding the pressure and shockwaves created by an explosion.
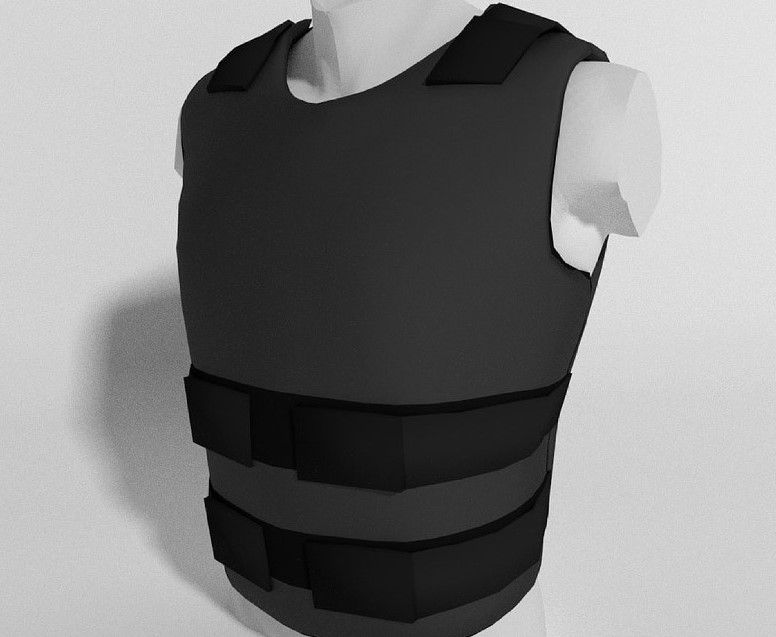
This is a significant development, as blast injuries are a leading cause of death in combat. Meaning that nanomaterial-enhanced body armour has the potential to save countless lives.
The technology behind these designs is constantly improving, with even more significant developments expected in the years to come. The exo-bulletproof material and nanomaterial advances are a major breakthrough and proof that technology can be used to protect and save lives.
This is crucial work in today’s world, as law enforcement officers, military personnel, and others who face injury or death from gunfire and explosions are relying on this small but vital manufacturing sector to protect them.
Photo credit: Danny H from Pixabay, Wirestock on Freepik, Picryl, Creazilla, Look&Learn, & Wikimedia