Nanotechnology Provides Custom-Made Raw Materials
Discover how nanotechnology is redefining raw material supply.
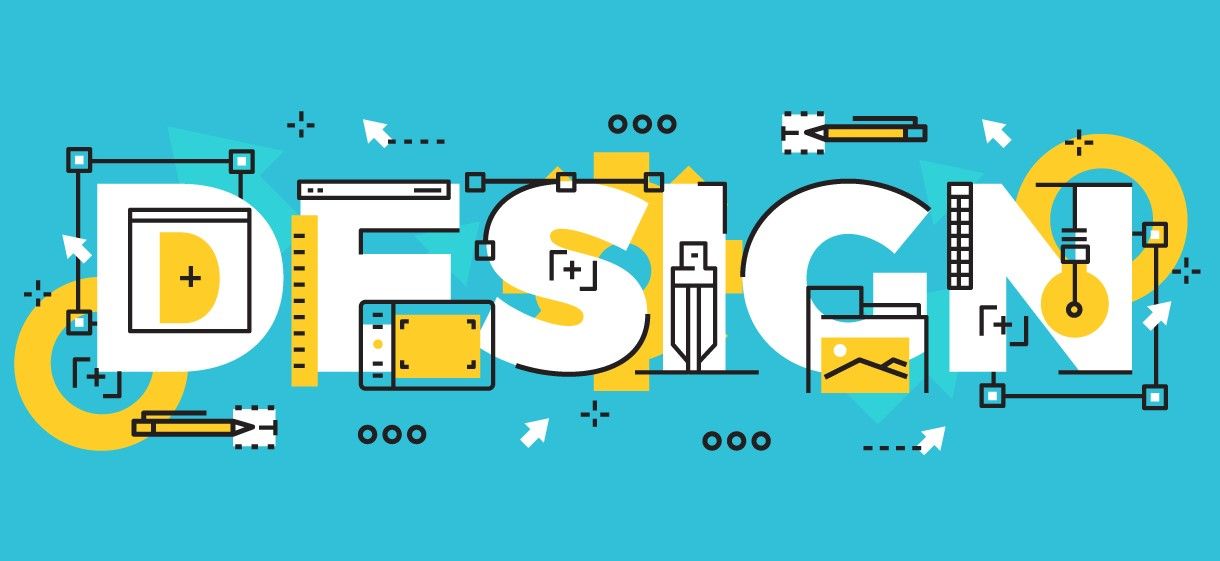
In today’s world, the concept of customization has expanded beyond tailored suits and made-to-order pizzas to now include raw materials themselves. Thanks to remarkable advances in nanotechnology, the manufacturing sector is experiencing a revolution that allows for the creation of composites given the exact properties required—to order!
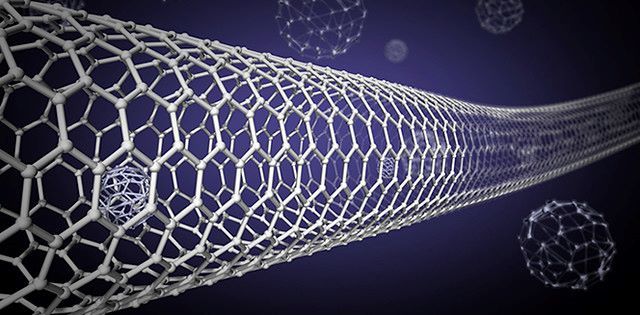
These custom designed raw materials can offer a wide range of benefits, including cost savings, environmental sustainability, and unique selling points.
The Rise of Customization in Manufacturing
Customization has long been a hallmark of high-quality products, offering individuals the ability to tailor goods to their specific preferences and requirements. From personalized cars to bespoke clothing, even credit cards with made-to-order designs, consumers have increasingly sought unique, specialised products. This demand for customization has now extended to the raw materials used in manufacturing processes—a move driven by advances in nanotechnology.
Nanotechnology: Redefining Raw Materials
Nanomaterials are made through the manipulation of bulk materials at the nanoscale level. A technological breakthrough which has opened up a world of possibilities for creating custom raw materials with enhanced properties. By engineering materials at the molecular level, researchers and manufacturers can design composites with precise characteristics tailored to the needs of specific applications.
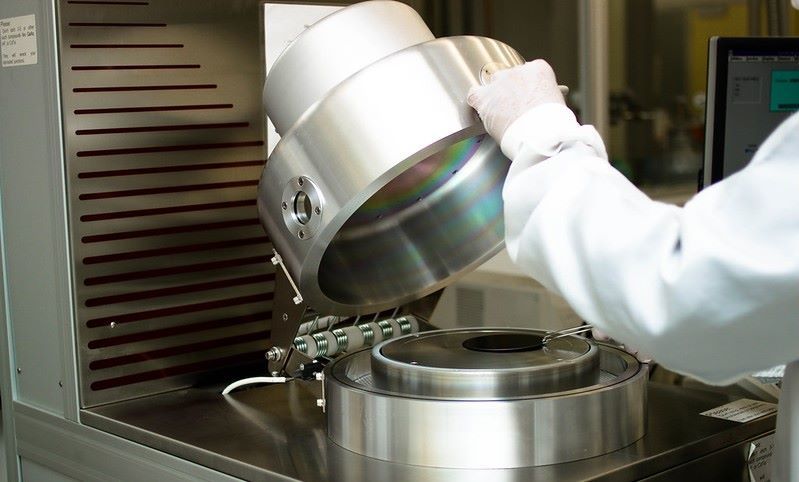
For example, one of the key advantages of nanomaterials is their exceptional strength-to-weight ratio, which allows for the development of lightweight yet incredibly durable materials. This means that by adding nanomaterials to a polymer, it can be made stronger, yet at the same time lighter. This property is especially valuable in industries such as aerospace, automotive, and construction, where weight reduction and added strength can lead to significant cost savings and improved performance.
Nanomaterial Composites for Sustainable Solutions
The use of nanomaterials in creating custom composites offers numerous environmental benefits, further contributing to the shift towards sustainability in manufacturing processes. By designing materials with optimized properties, manufacturers can reduce waste, energy consumption, and resource depletion, leading to a more eco-friendly production cycle.
Furthermore, the nanomaterials themselves can even be made from recycled materials.
Nanomaterial Composites for Cost Savings
In addition to their environmental benefits, custom-made raw materials using nanotechnology offer significant cost savings for industry.
For example, the inclusion of nanomaterials can replace conventional feedstocks as nanomaterials can often do more with less.
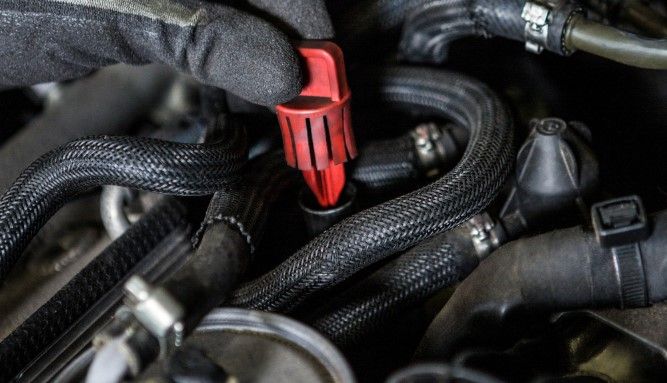
For example, in the manufacture of vehicle tyres, the use of a small amount of carbon nanotubes as a raw material means that significantly less carbon black is required. This means that switching from a bulk raw material to one based on nanotechnology can actually reduce input costs.
Nanomaterial Composites for Improved Performance
Furthermore, the unique properties of nanomaterials, such as superior durability, thermal conductivity, and chemical resistance, can lead to improved performance in end products. Whether it is designing lighter and more fuel-efficient vehicles or creating high-performance electronics, custom-made nanomaterial composites enable manufacturers to stay at the forefront of innovation and deliver products that meet the evolving needs of consumers.
Related articles: Nanomaterial Composites and the Aerospace Industry or Raw Material Advantages: Bulk vs Nanoscale
Nanomaterial Composites for Unique Selling Points
By dispersing nanomaterials within a polymer matrix, the resulting nanocomposite material exhibits enhanced mechanical strength, thermal stability, and electrical conductivity.
For example, vehicle engines often contain a small rubber tube which carries the fuel from one engine part to another. By adding nanomaterials into the rubber when it is being made the tube it lasts longer and prevents the build-up of static electricity which could cause a catastrophic explosion. The result is a safer, longer lasting vehicle made with a rubber fuel tube with a unique selling point.
Nanomaterial Composites for Across Industries
The possibilities for custom-made raw materials using nanotechnology are virtually limitless, with applications spanning a wide range of industries. Construction materials, aerospace and automotive parts, resins, metals, rubbers, dyes, coatings, cosmetics, medicines, textiles, ceramics, electronics, glass, plastics, and even concrete can all be improved, given unique selling points, made more environmentally sound, made cheaper, or more durable with the inclusion of nanomaterials.
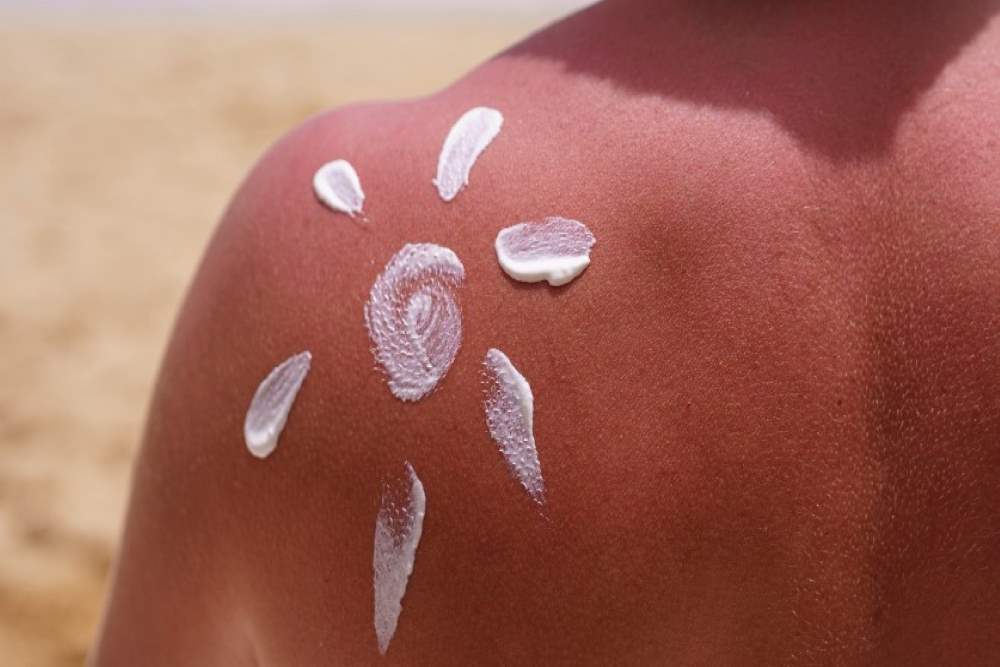
Nanomaterials for a Custom-Made Future
The emergence of tailored raw materials through nanotechnology represents a pivotal moment in the evolution of manufacturing processes. It is a sea-change in how products are made through the incorporation of nanomaterials and their unique properties and a way in which manufacturers can create specialized composites that offer cost savings, environmental benefits, and unparalleled performance across industries.
By embracing customization and harnessing the power of nanotechnology, manufacturers in multiple industries have the opportunity to pave the way for a more efficient, personalized economy. One that is manufactured with custom-made raw materials.
If you would like to more about how to design your own nanomaterials with the properties that your manufactured products require, then contact POLYMER NANO CENTRUM.
POLYMER NANO CENTRUM (which hosts this webpage) manager one of Europe’s leading research centres for the application of nanomaterials in industry. They have already custom designed hundreds of nanotechnologies to provide their clients with desired selling points and cost savings.
Contact them at info@polymernanocentrum.czor call +420 233 371 850 to find out how your products can be improved.
Photo credit: Freepik, Newelement, Peoplecreations, Flickr, & Divya Desai