Modern Composites Gain Crack Resistance with Nanostitching
MIT nanotechnology researchers use carbon nanotubes to bond materials into a more durable composite with added crack resistance.
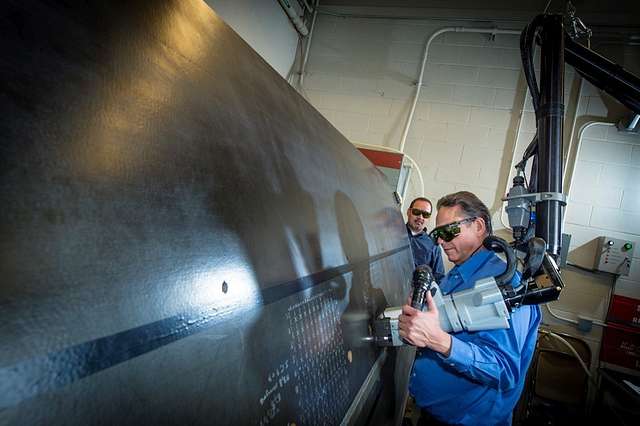
Whether it is for building armour, bridges, buildings, or ships – engineers are constantly looking for strong, robust materials that do not have the disadvantage of being heavy.
This is especially true for modern engineering projects, such as aeroplanes, boats, or space craft, which require minimal weight for fuel efficiency, but also require sufficient durability and sturdiness to remain in one piece.
To solve this problem, advanced manufacturing materials have been developed made from high-performance fibres embedded in polymer sheets. When layered on top of one another and pressed together, the sheets form a formidable composite combining low weight with exceptional strength.
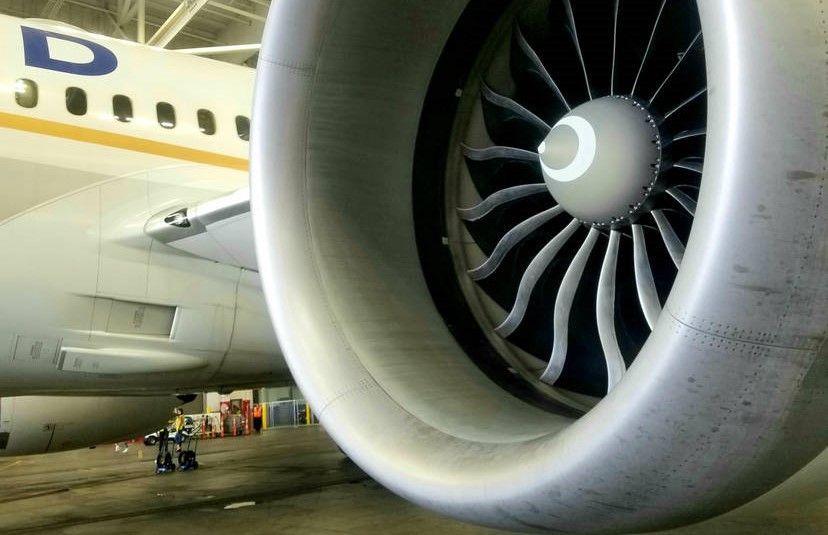
However, the gap between the layers contains a significant weakness, as the polymer ‘glue’ holding the sheets together can be prone to cracking. As this bond is hidden deep inside the composite, these fissures can easily remain unseen, spreading along stress lines further weakening the material and potentially leading to the failure of the overall structure.
To avoid these cracks from forming, nanotechnology researchers from MIT have employed a technique they called ‘nanostitching,’ which involves chemically growing miniature forests of carbon nanotubes between composite layers. This keeps the layers from ripping or shearing apart as the minuscule, closely spaced fibres function as a superstrong bond - holding the layers together.
“Just like phyllo dough flakes apart, composite layers can peel apart because this interlaminar region is the Achilles’ heel of composites,” explains Prof. Brian Wardle who played a leading role in the research. “We’re showing that nanostitching makes this normally weak region so strong and tough that a crack will not grow there. So, we could expect the next generation of aircraft to have composites held together with this nano-Velcro, to make aircraft safer and have greater longevity.”
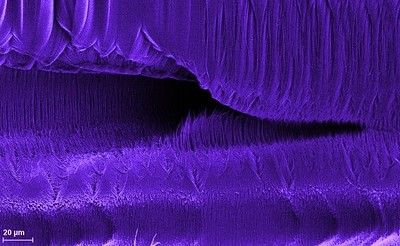
Carbon nanotubes are tiny tubes of carbon, so small than billions of them can be placed on an area as small as a little fingernail. But pound for pound, carbon nanotubes are the strongest materials known to science, and when formed into a densely packed forest, they can form a strong bond between two materials.
“To grow the nanotubes, the team used a process of chemical vapor deposition to react various catalysts in an oven, causing carbon to settle onto a surface as tiny, hair-like supports,” the MIT press release describes. “The supports are eventually removed, leaving behind a densely packed forest of microscopic, vertical rolls of carbon.”
These forests have been known for many years, but the benefits of using them as a bonding tool for composites is only now being appreciated. As the report notes, “In their new study, the engineers took a more in-depth look at the between-layer region in composites to test and quantify how nanostitching would improve the region’s resistance to cracks. In particular, the study focused on an advanced composite material known as thin-ply carbon fiber laminates.”
“This is an emerging composite technology,” explains Wardle, “where each layer, or ply, is about 50 microns thin, compared to standard composite plies that are 150 microns, which is about the diameter of a human hair. There’s evidence to suggest they are better than standard-thickness composites. And we wanted to see whether there might be synergy between our nanostitching and this thin-ply technology, since it could lead to more resilient aircraft, high-value aerospace structures, and space and military vehicles.”
Tests have now proven the strength and crack resistance of the new polymer-nanomaterial hybrid. Creating an advanced composite of sixty layers, each consisting of strong horizontal fibres embedded in a polymer sheet but measuring only three millimetres thick. A nanotube forest was then transferred and adhered between the central layers before being cured.
A crack was then made on the edge of the composite, exactly between the two middle layers.
“In fracture testing, we always start with a crack because we want to test whether and how far the crack will spread,” explains Prof. Carolina Furtado who led the experiments.
Then the nanomaterial bond was assessed to see if the layers would easily separate – a phenomenon known as ‘delaminating.’
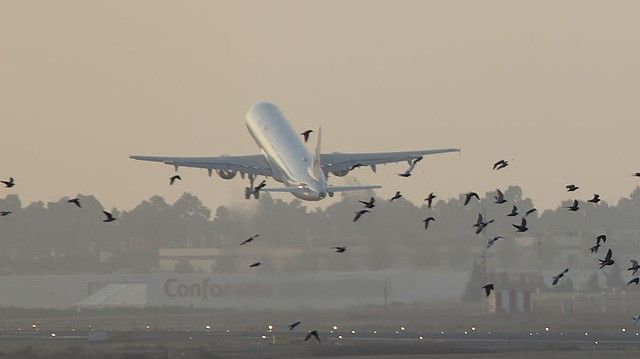
“There’s lots of ways you can get precursors to delamination, such as from impacts, like tool drop, bird strike, runway kickup in aircraft, and there could be almost no visible damage, but internally it has a delamination,” says Wardle. “Just like a human, if you’ve got a hairline fracture in a bone, it’s not good. Just because you can’t see it doesn’t mean it’s not impacting you. And damage in composites is hard to inspect.”
The tests covered the three main ways in which delaminating occurs in modern composites – the layers peeling apart at the site of a crack, the layers sliding apart, or a combination of both. When the team measured the force needed to get the layers to peel or shear in two, they observed how when nanostitching was applied the composites were 62 per cent tougher as well as performing better at preventing the crack from spreading.
“The authors have demonstrated that thin plies and nanostitching together have made significant increase in toughness,” observes Standford University’s Prof. Stephen Tsai. “Composites are degraded by their weak interlaminar strength. Any improvement shown in this work will increase the design allowable, and reduce the weight and cost of composites technology.”
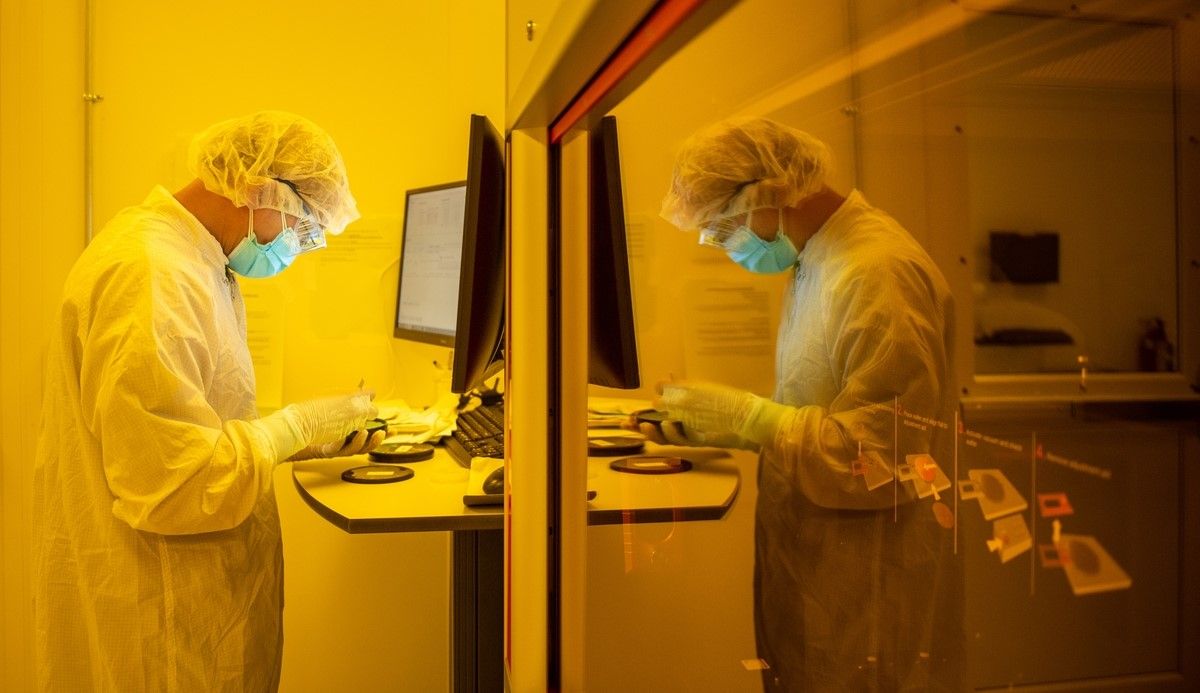
While nanotechnology already play a role in all sectors of the economy, the use of nanomaterials to strengthen and lighten conventional composites is a truly broad application. Without requiring a major overhaul of how these materials are manufactured, carbon nanotubes used as a nanostitching glue can be ‘dropped’ into various production processes. Aircraft, spacecraft, high performance cars, and boats, can all benefit from this discovery.
As the study, now published in the journal Applied Materials & Interfaces, notes, “The findings presented in this work extend to industries that rely on carbon-fiber advanced composites, including mass-specific applications such as aerospace, wind, automotive, and some infrastructure applications, where lightweight, durable materials are critical for improving structural efficiency.”
The discovery could even save money, as it would extend the lifespan of aircraft and increase safety.
“This opens a big window of opportunity,” say Furtado. “You could have selective reinforcement of problematic areas, to reinforce holes or bolted joints, or places where delamination might happen.”
“This is a new composite technology,” concludes Wardle. “Turbocharged by our nanotubes.”
Photo credit: Flickr, Wikimedia, Deviantart, Picryl, & Rawpixel