Industry Embraces Additive Manufacturing with Nanotechnology
Manufacturers are looking to 3D Printing with nanomaterials to gain a competitive edge.
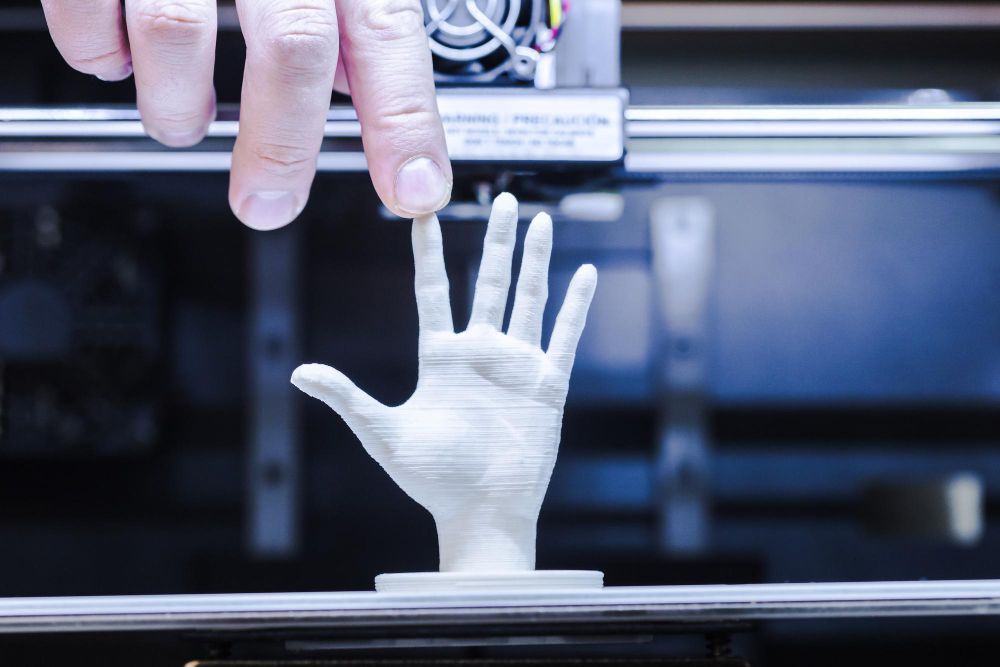
Nanotechnology is already influencing the manufacturing sector, with hundreds of thousands of products using nanomaterials to boost or add new properties. However, it may be that the greatest advantages to be had from nanomaterials are from their inclusion in 3D printing or additive manufacturing.
As a recent study published in the journal Nano Futures, highlights, “The Additive Manufacturing of polymer nanocomposites is a growing area of research because nanomaterial additives can enhance the mechanical, electrical, and other properties for end-use applications.” Adding that, “… the use of nanomaterial inclusions can also enhance the Additive Manufacturing processes themselves.”
Because of this, 3D printing has already been adopted for a number of manufacturing processes, as it can produce complicated geometries and multi-material structures without the restraints and costs of traditional subtractive manufacturing techniques (such as machining) or formative techniques (such as forging and casting).
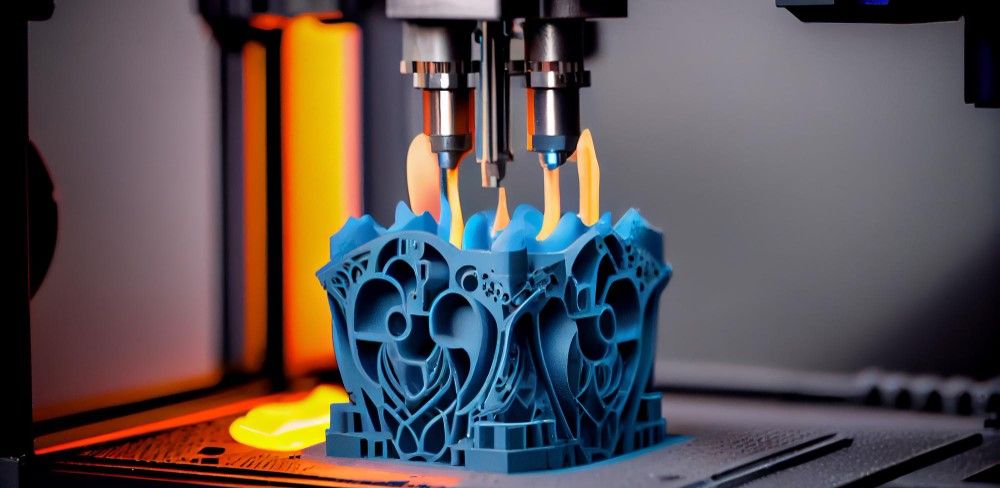
Moreover, additive manufacturing processes can utilise the effects and qualities of nanomaterials to fabricate composites with in-built electrical, mechanical, optical, thermal, magnetic, and biological capabilities. This is having a major impact on the manufacture of energy storage devices, sensors, photonic devices, microelectromechanical systems, and other electrical and electronic components.
For instance, despite its mechanical brittleness and poor biocompatibility, the acrylic polymer polymethylmethacrylate (PMMA) has been utilised in the surgical fixation of artificial joints for decades. However, by adding hydroxyapatite (HAp) nanoparticles and carbon nanotubes to the polymer, these faults are fixed, and the resulting matrix is enhanced for biomedical applications.
Similar progress has been made in the 3D printing manufacture of higher performance dielectric capacitors sought by the electronics sector for, among other things, wind turbines and electric cars.
As the industry journal Azo Nano reports, “by 3D printing poly(vinylidene fluoride–chlorotrifluoroethylene) (P(VDF–CTFE)) incorporated with barium titanate (BaTio3) nanowires, the high shear environment from the printing process aligned the nanowires in the print direction and gave an energy density 55% higher than that of the equivalent ‘non-aligned’ nanocomposite at the same level loading.”
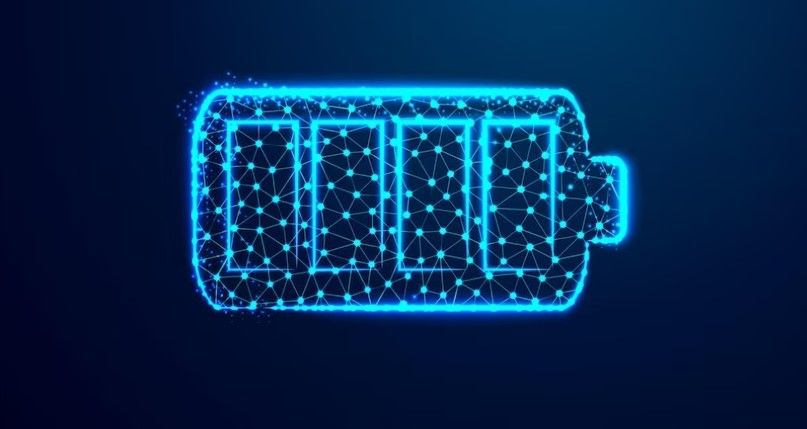
Advances such as these are now playing a significant role in modern warfare, placing the application of nanomaterials in 3D printing at the forefront of military research and future military production.
For example, when developing novel systems, additive manufacturing has been particularly helpful since it enables programs to produce complicated components more quickly than would be possible with conventional manufacturing procedures. 3D printing also allows for the creation of metals with high entropy that are extremely robust and resistant to wear and tear. These materials are extremely useful for cutting-edge military technologies such as hypersonic missiles.
For example, scramjet propulsion systems are used in a variety of hypersonic power systems but require complex chambers that are difficult to produce with conventional techniques. By 3D printing the parts, military researchers can make much faster progress.
As a recent report in the industry journal Defense News explains, “Additive manufacturing would allow scramjet components to be made from high-temperature metals in a way that eliminates the need to have complex welds or brazing joints. Those joints need to be tested to ensure they’re sound … but a component made via additive manufacturing that doesn’t have those joints won’t need such testing.”
“Being able to incorporate additive manufacturing is enabling us to manufacture complexity that has not been able under the subtractive, traditional manufacturing methods,” says Keith DeVries, deputy director of the Office of the Secretary of Defense’s Manufacturing Technology Program.
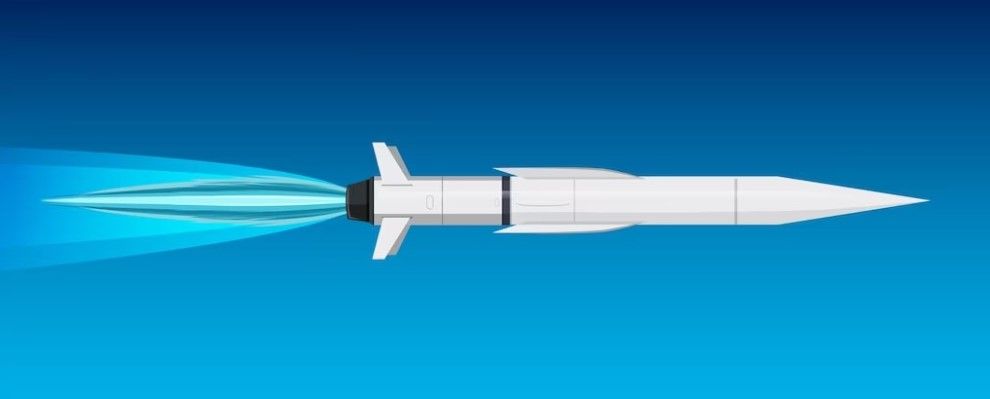
Another area where nanotechnology is combining with 3D printing is in the polymers used in body armour. The inclusion of nanomaterials, improves impact protection, lowers weight, can increase functionality in extreme temperatures and allows for better resistance to scratching and cracking.
Additionally, the use of 3D printing allows for manufacturing on demand very close to the frontlines. Particularly as 3D design files can be saved in a virtual library where they may be accessed and printed as needed because they are printed using a 3D model as either a CAD or STL file.
Significantly, unlike conventional production techniques, additive manufacturing has the advantage of requiring less storage space for inventory – a common challenge close to the battlefront.
Much like 3D printing, nanotechnology has been the subject of intensive research and development in recent years. Both are now revolutionising a wide range of industries, and in many cases, they have already done so. Their constructive collaboration is a logical next step in each of their advancement and holds the promise of having an equally innovative and profound effect.
Photo credit: Vecstock on Freepik, Freepik, Fabrikasimf, & Freepik