What Makes a Good Raw Material for Drone Production?
Discover the elements that make drone manufacture a science.
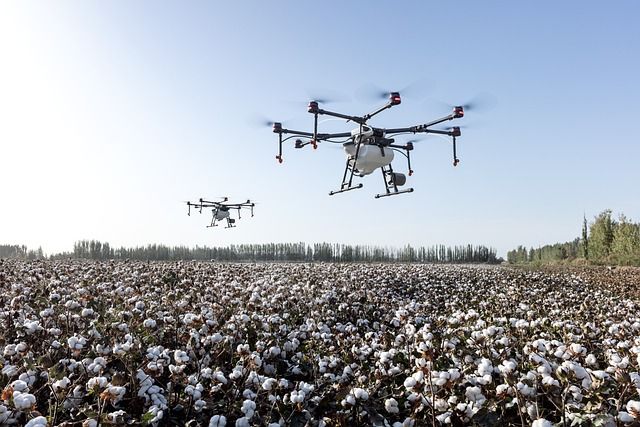
Drones are finding more and more practical uses in every walk of life.
They are a key part of military intelligence gathering, are used in surveillance, wildlife photography, as a hobby and in Hollywood, while numerous companies are looking to use drones for the delivery of anything from Amazon to Domino’s Pizza.
However, for drones to achieve these goals, technology must progress to the next level.
At the heart of all aerospace design is the need to keep weight low enough to enable lift, yet strong enough to carry a payload of people, goods, fuel, sensors, cameras, and the technology needed to fly. Reducing weight also reduces the fuel required to fly, extending range and flight times.
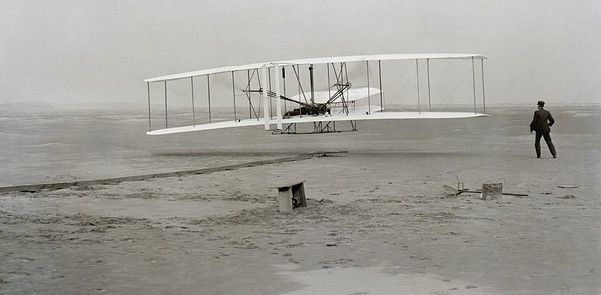
The ‘go-to’ raw materials in conventional, piloted aviation, are aluminium and titanium. While neither of these metals in as cheap as steel, they are relatively low weight with excellent strength, while maintaining sufficient flexibility to allow for the stresses and strains of flight.
As aeroplane design improves, an increasing number of composite materials ae being applied to specific aircraft parts – most commonly carbon fibres or carbon fibre-polymer composites.
A Raw Material with Low Weight
Essential to their use in aerospace production is carbon fibre’s low weight. For this reason, drones are almost exclusively made from carbon fibre or carbon fibre composites.
Water has a density of 1g per cubic centimetre, and while carbon fibre may seem heavy with a density of around 2g/cm3 the use of a material matrix embedded into the fibres to create a composite reduces weight.
“Carbon composites are usually composed of 35% to 45% carbon fiber,” explain the carbon fibre experts at Hexcel. “So, the overall density of the composite is in the range of 1.3 to 1.6 g/cm3.”
When compared to density of aluminum (2.7 g/cm3) and titanium (4.5 g/cm3, carbon fibre composites have a very low density of between 1 to 1.4 g/cm3.
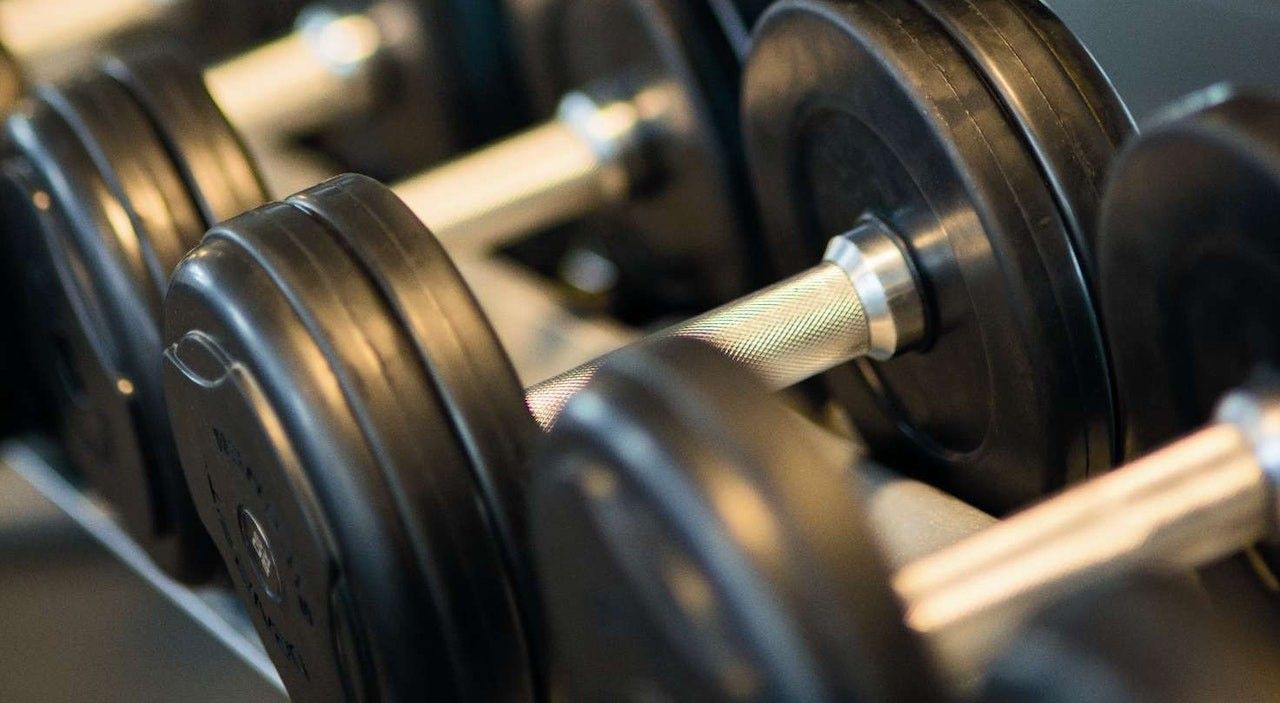
A Raw Material with Good Strength
A material’s low weight means nothing if it is not also strong. Foams, for example, are exceptionally light, but also very weak.
Carbon fibre is relatively light, but also strong enough to carry a significant load. It even performs well when compared to some metals, as metals are more likely to deform before breaking due to plastic deformation. For example, a metal band may bend or buckle under stress, whereas a carbon fibre band is more likely to remain rigid.
As the Hexcel experts state, “Stiff materials that keep their shape under load are better than materials that deform permanently, and they should withstand high flight loads and not break. For reference, aluminum has a specific strength of 115, titanium has a specific strength of 76, and carbon composites have a specific strength of 785.”
A Raw Material with High Specific Modulus
But more than being just lightweight and strong, any raw material used to make a drone must also have the correct stiffness-to-weight ratio, more commonly known as specific stiffness or specific modulus.
Rubber has a low specific modulus. If a rubber band is stretched between your fingers and a load is applied, the band will stretch downwards.
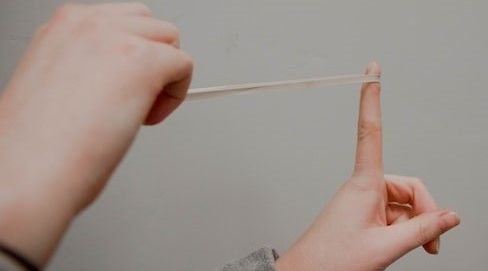
Raw materials used to make drones (or any aircraft) need to be rigid enough to carry a load and still be able to fly.
“The higher the specific stiffness, the better the material for a given stiffness critical structural application,” notes Hexcel. “High specific stiffness materials are generally used in aerospace. For reference, titanium has a specific stiffness of 25, aluminum has a specific stiffness of 26, and carbon composites have a specific stiffness of 113.”
It is this combination of low weight, good strength, and stiffness that makes carbon fibre the number one raw material for UAV production.
A Raw Material to Improve them All
Nanomaterials have become increasingly influential in manufacturing over the past two decades. What began as a lab-created substance with only theoretical applications is now a fully functioning, economically viable, industrial raw material with practical uses in almost every sector of the economy.
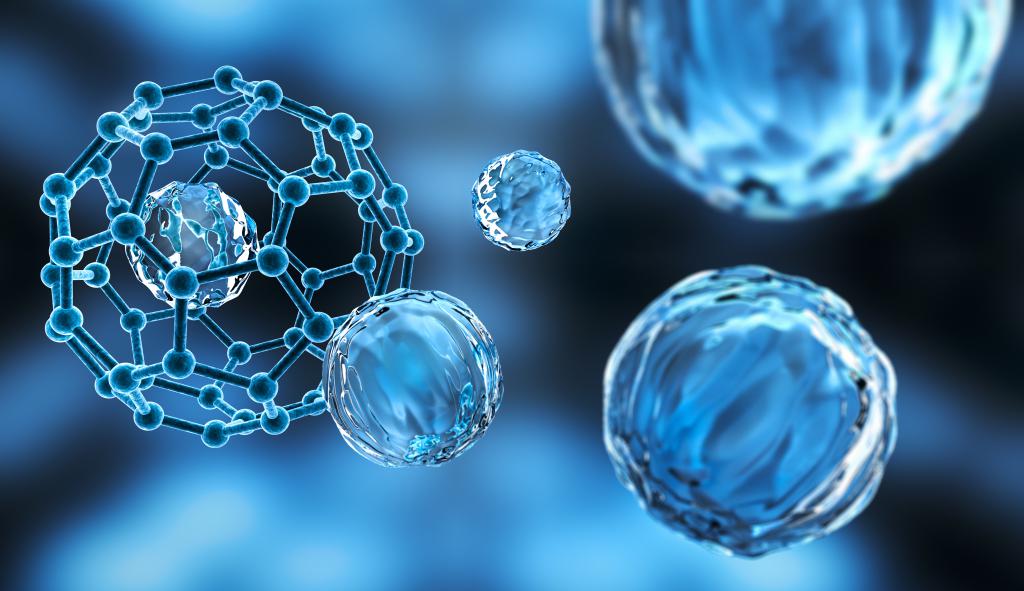
Today, nanotechnology influences the production of ceramics, glass, construction materials, electronics, metals, pharmaceuticals, coatings, plastics, textiles, and, with increasing importance, the manufacture military hardware.
As discussed earlier in this article, key aspects of raw material selection for the production of drones include low weight, good strength, and specific modulus. All of these properties can be influenced with the application of nanotechnology.
To find out more about how nanomaterials can be used as an industrial additive to improve polymers such as epoxy resins, PVC, plastic regranulate, methyl methacrylate, polyester and more visit Polymer Nano Centrum.
Composites offer several advantages for lightweight aerial vehicles, and those advantages are only increased with the inclusion of the right nanotechnology.
Photo credit: DJI Agras from Pixabay, Kenny Eliason on Unsplash, Wikiimages, & Freepix