Top Techniques for Composite Production for UAVs
Constructing better UAVs can now be achieved with these polymer composite production techniques.
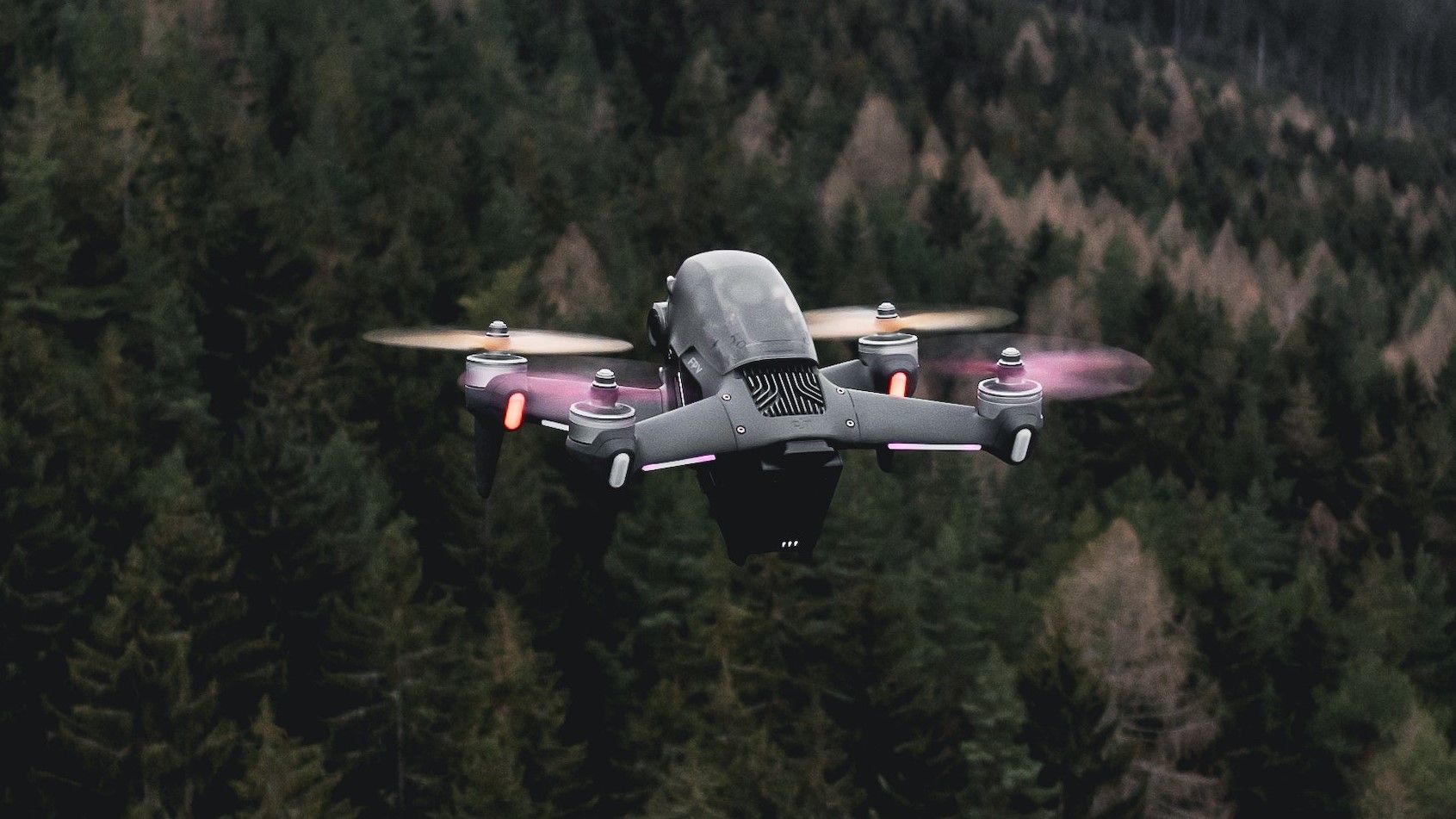
Unlike popular hobby drones, modern military UAVs (Unmanned Aerial Vehicles) cannot be built with any old plastic.
Well, that is not exactly true. They could be built from anything, but the loss in performance, durability, and lifespan, would not make economic or practical sense.
UAVs carry expensive payloads, first-rate technology, and military information which in the wrong hands could cost many lives. So, investing in a military drone’s proper construction makes good sense on every front.
At this point it is also worth mentioning that all raw materials and drone designs used need to pass the relevant local safety authority before flying commences Federal Aviation Administration (FAA) in the US and the European Union’s Aviation Safety Agency (EASA).
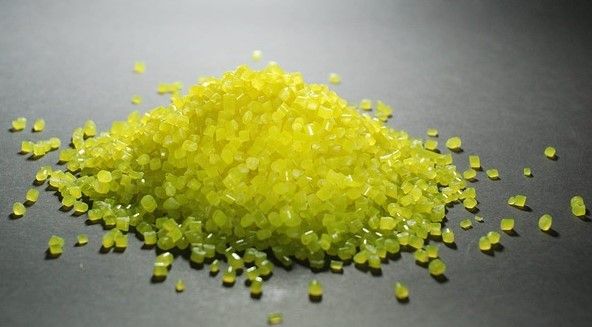
For this reason, carbon fibre composites – despite their relatively high cost – are the most commonly used raw materials for the production of military drones. As the carbon fibre experts at Hexcel note, “Upfront costs per unit weight [of carbon fibre] are higher than most metals, but the total lifecycle cost of carbon composites is lower.”
These costs include construction, maintenance, inspections, operational costs, refurbishments, and end-of-life retirement costs. Of note is that unlike metals, polymer composites are less prone to corrosion, are more fatigue resistant, and less likely to crack over repeated cycles.
Polymer composites are also more easily repaired with patches than metal structures.
Against this background, here is a brief outline of the various techniques used to prepare flight-grade carbon fibre materials.
Prepregs
One of the most common aerospace composite construction approaches is the prepreg. For carbon fibre composites this entails pre-impregnating a sheet of carbon fibre with resin or epoxy.
At room temperature, these pre-cut boards are pliable, and so can be flexed and formed into a desired shape. Heating the carbon fibre-epoxy composite cures and hardens the prepreg, although sometimes uncured boards are stacked and then laminate cured.
Thermoplastic matrix materials
Like epoxy resin composites, thermoplastic matrix materials can be cut and formed into prepregs. While thermoplastic systems are usually more expensive than epoxies, the extra money provides a number of advantages.
These include:
· As thermoplastic materials do not cure (they crystalize), they can be re-formed or repaired via heating (unlike epoxies).
· Epoxy resin composites need to be kept in the freezer to avoid unwanted curing.
· Even inside the freezer, epoxy resin composites still have a shelf life, whereas thermoplastics will last almost indefinitely.
Laminates
Laminates are most commonly fabricated from hand lay-up processes. They are typically fabricated from prepreg plies which have been cut to size and then laid down and stacked on a tool surface.
While the simplicity of the process allows for flexibility in design, it is not a very efficient large-scale production process, and so is more likely to be used for making prototypes.
Since the beginning of the century, Automated Tape Lay-up (ATL) and Automated Fibre Placement (AFP) machines have been developed to speed up the process and to reduce labour costs. With the addition of computerised systems, production quality can be improved while also streamlining the transfer of computer-aided design (CAD) into a finished laminated configuration.
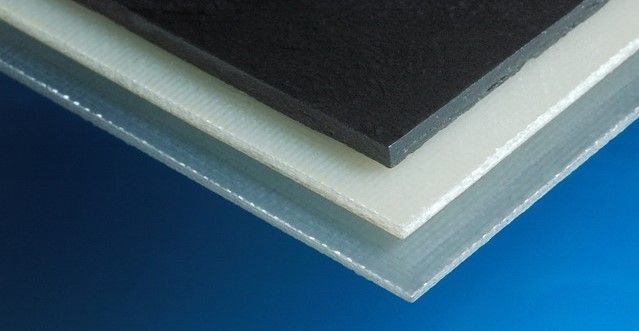
These machines help to create a more uniform and reliable end product in a mass-produced, repeatable operation – much as computer-aided machining (CAM) processes are used for machined parts. Similar automated systems used in UAV production include thermoforming, ply cutting, filament winding, pultruded composite beams, and fibre patch placement.
Direct processing methods
Instead of pre-impregnating a fibre sheet with resin, some composites are formed with direct processes as doing so can save both time and money. For example, resin can be infused onto a dry laminate or fabric.
For this to happen, a fibre architecture is laid down in a tool before resin is infused into the structure. A mould is then sealed onto the fibre preform and resin is either injected under pressure into the tool using a Resin Transfer Moulding (RTM) process or pulled into the tool using a Vacuum Assisted Resin Transfer Moulding (VARTM) process.
Both of these processes occur at high temperatures to maintain resin viscosity before cooling allows the resin to cure in place.
Additive Manufacturing
Often called 3D-printing, additive manufacturing builds up layer upon layer of material to create a single-piece structure. While the process is not the cheapest, the reduction in connecting parts improves overall body strength.
Companies are continuing to research and utilize the numerous additive manufacturing technologies, including sophisticated robotic systems, which have been created over the years. This has resulted in complex three-dimensional geometries being made with continuous fibre.
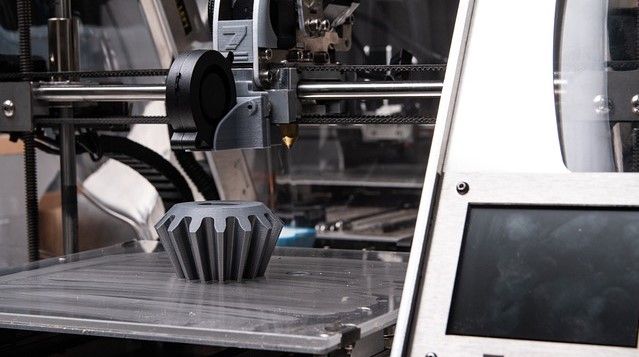
Composite structures are also being produced using additive manufacturing techniques which incorporate chopped fibre. Chopped carbon fibre can be utilized in both fused deposition modelling (FDM) and selective laser sintering (SLS) to produce products that are stiffer, stronger, and lighter than ones made solely of plastic. This approach works especially well for brackets, ducts, and handles since they can be made without the use of special tools, which significantly reduces costs.
Electromagnetic frequency
One advantage of composites is that they can be tuned to absorb specific electromagnetic frequencies while letting others pass. This makes them ideal for use in the fabrication of radomes which protect the receiving and transmitting antennas against the elements. Without these antennas, drones cannot fly.
For military UAVs, the ability to block certain electromagnetic frequencies helps enable the aircraft avoid detection or prevent jamming of the signal – a common defence system against enemy drones.
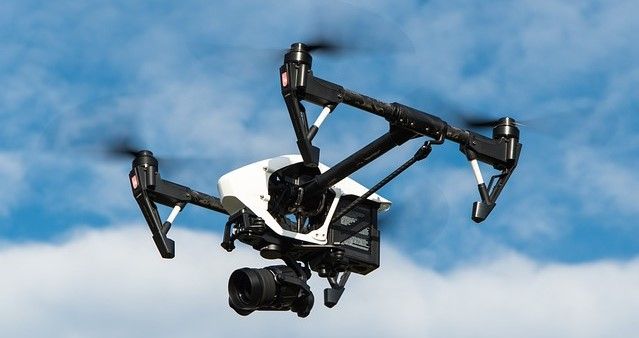
This list is far from exhaustive and as developments are made new raw materials and improved designs are certain to come to light.
As a whole, the UAV sector is still in its infancy, with its military value only now being truly highlighted in the Ukraine/Russia conflict. How far UAV production will expand if commercial deliveries become commonplace, or if private drone flights become the norm is unclear.
However, the dream of lower delivery costs, improved anti-crime methods, and a stronger national defence all make for a promising outlook for the sector. One that can only be enhanced with improved raw material and fabrication techniques.
As one polymer composite expert notes, “Carbon composite materials, honeycomb core structures, additive manufacturing, and dielectric tuned materials are key parts of this industry today and will continue to enhance the functionality and efficiency of these vehicles in the future.”
Photo credit: Thomas Ehrhardt from Pixabay, Adrian Malec, ZMorph Fab 3D printer, Adrian Malec