Polyimide Films with Customised Thermal Performance
Novel nanomodification process now enables manufacturers to adjust thermal resistance on demand.
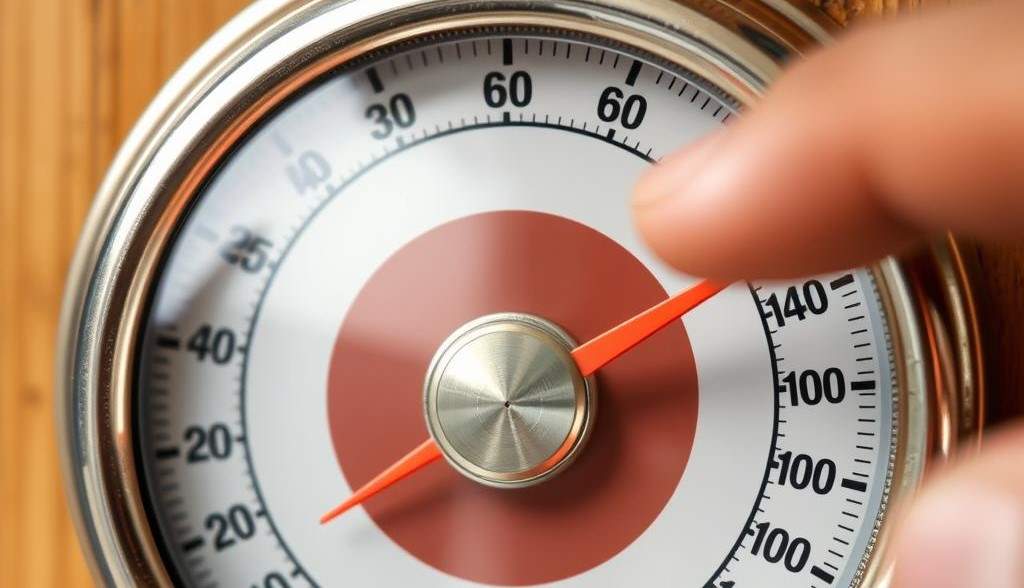
Polyimide films are the unsung heroes of high-performance materials. Known for their exceptional thermal stability, mechanical resilience, and chemical resistance, they’re a go-to choice for manufacturers of products for aerospace, electronics, and automotive industries. But today, nanotechnology is taking these films even further—with nanomaterial scientists tailoring their behaviour to meet exact performance needs.
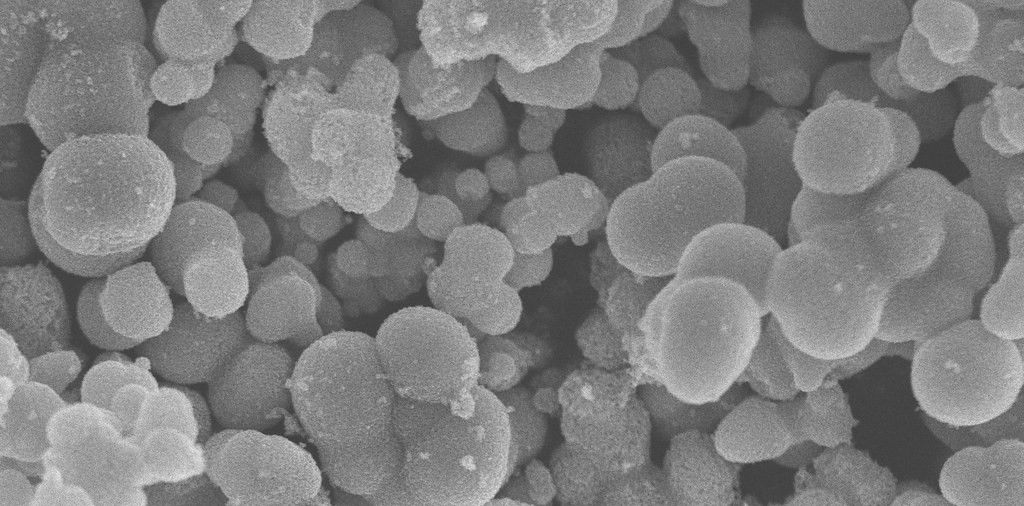
One example of the successful application of nanotechnology in these raw materials was recently published in the journal Frontiers in Materials. Here the researchers, led by Assistant Professor Ahmad Ashraf, were able to selectively enhance key thermal properties of polyimide films, such as thermal stability and glass transition temperature (Tg) by embedding aluminium oxide (Al₂O₃) and zinc oxide (ZnO) nanoparticles into the polyimide matrix.
While the research may sound like a niche discovery in a small scientific field, it actually has a far-reaching impact on polymer manufacturing and is further evidence of how everyday polymer products can be improved with boosted properties and unique-selling points.
These advances are achieved by nanocomposite engineering: introducing tiny amounts of carefully selected nanoparticles to shift material performance without disrupting its fundamental structure. This is in contrast to traditional approaches to improving thermal resistance which often add weight or compromise other properties.
In this instance, the nanotechnology can be applied to products such as flexible electronics or heat-shielding components—advanced polymer materials that need to perform reliably in extreme environments.
The nanotechnology researchers chose to use aluminium oxide (Al₂O₃) and zinc oxide (ZnO) nanoparticles as they were already well-known ceramic nanomaterials which had been proven to be especially effective:
· Al₂O₃ (aluminium oxide) is a thermal conductor and stabiliser that improves degradation resistance.
· ZnO (zinc oxide) contributes UV-blocking properties and significantly increases glass transition temperature (Tg), enhancing rigidity at high temperatures.
In the research the team fabricated a series of polyimide films containing 3%, 5%, 7%, and 9% volume concentrations of Al₂O₃ or ZnO nanoparticles. These nanocomposite films were then subjected to a wide range of thermal and structural characterisation techniques, including:
· FTIR and NMR spectroscopy to confirm chemical structure.
· WAXRD and SEM to observe nanoparticle dispersion and crystallinity.
· TGA (Thermogravimetric Analysis) for decomposition temperatures.
· DMTA (Dynamic Mechanical Thermal Analysis) for glass transition behaviour.
· and isothermal TGA to test performance under prolonged high-heat exposure.
These tests on the nano-modified polyimide films had impressive outcomes, with experiments specifically noting:
· Thermal Stability: Adding Al₂O₃ nanoparticles increased the onset of degradation temperatures. For instance, the 9% Al₂O₃-loaded film showed less than 2% weight loss after 35 minutes at 400 °C—better than the 2.6% loss in pure polyimide.
· Glass Transition Temperature: The Tg of the pure film was ~293 °C. By adding 5% Al₂O₃, this increased to 357 °C. Even more dramatically, 5% ZnO raised Tg to 384 °C—suggesting that ZnO creates tighter chain networks, increasing stiffness at high temperatures.
· Nanoparticle Dispersion: SEM and WAXRD confirmed reasonably uniform distribution, though ZnO tended to show minor aggregation at higher loadings.
These results show that Al₂O₃ and ZnO can be used not only to improve polyimide films but to customise them for different needs: Al₂O₃ for heat endurance; ZnO for thermal rigidity.
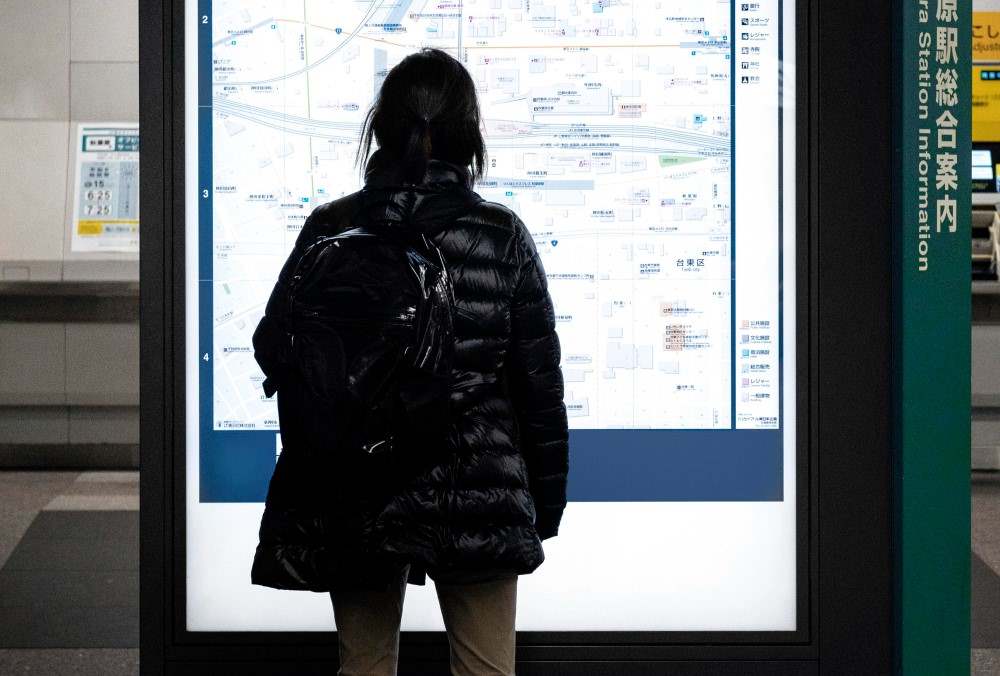
This kind of targeted thermal tuning will have a strong impact on manufacturing, and opens the door to smart material selection for high-value sectors, such as:
· Aerospace: weight-sensitive, heat-resistant films for insulation and shielding.
· Electronics: substrates or casings that can withstand heat while maintaining dimensional stability.
· Automotive: heat-tolerant components either under the bonnet or near heat sources.
· Solar and outdoor applications: improved UV resistance and high-Tg performance in exposed conditions.
Importantly, the methodology uses commercially available nanoparticles and scalable film-processing techniques, increasing its potential for real-world manufacturing.
This breakthrough underscores the enormous potential of nanotechnology to unlock next-generation performance in polymer-based materials. By integrating just a small fraction of Al₂O₃ or ZnO nanoparticles, researchers have shown that it’s possible to precisely control the thermal behaviour of polyimide films—without compromising their structure, weight, or manufacturability.
For material developers and manufacturers, this means access to smarter, leaner, and more efficient polymers tailored to demanding environments. Whether for thermal shielding in aerospace, miniaturised electronics, or robust automotive components, nanocomposite-engineered polyimides offer a compelling route to competitive advantage.
Fellow nanomaterial specialists see this kind of research not as an isolated success, but as part of a wider trend. For example, the team at POLYMER NANO CENTRUM are consistently finding new ways to apply nanotechnology in the polymer industry. Based just outside Prague, the company (which hosts this website) know that nanomaterials are no longer just experimental substances for the laboratory. Instead, they have become practical tools for solving real-world industrial challenges.
Using nanotechnology not to reinvent the wheel, but to make it run faster, longer, and smarter.