Nanotechnology Rewrites the Rules for Raw Materials
Is this the end of the strong-vs-flexible trade-off for sourcing industrial polymers?
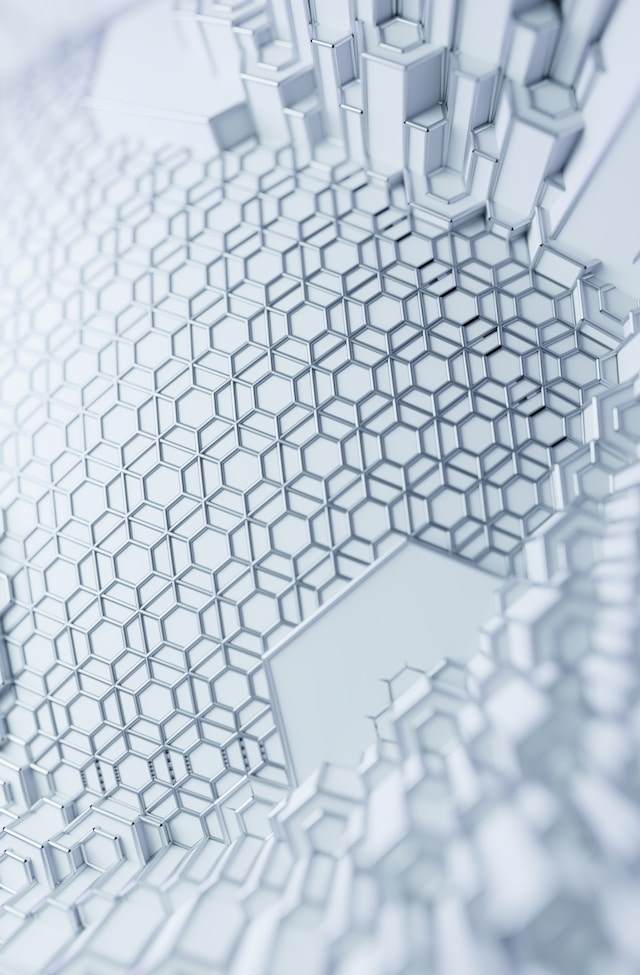
Industrial feedstocks are chosen based on their dominant properties, but this often comes at the expense of other qualities.
Steel, for instance, is strong and robust, but lacks flexibility and is heavy. Polyethylene is lightweight and cheap, but relatively weak and not heat-resistant. Carbon fibre is strong and lightweight, but expensive and brittle. Rubber is flexible but has low strength and degrades over time.
But now a team of nanotechnology researchers from MIT, may have removed this trade-off through the smart application of synthetic printable metamaterials.
Related articles: Reinventing Wood with Nanotechnology or Nanomaterials Create a New Class of Lubricant
Metamaterials are engineered materials designed to have properties not found in naturally occurring substances. They achieve this by structuring materials at the nanoscale in a way that affects how they interact with physical forces, often with an ideal to make materials stronger.
Yet even with metamaterials, there is usually a compromise—the stronger a material is made, the more brittle it becomes.
But the MIT team may have resolved this issue with a blend of cheap polymers formed correctly at the nanoscale. As the university press release explains, “The key to the new material’s dual properties is a combination of stiff microscopic struts and a softer woven architecture. This microscopic ‘double network,’ which is printed using a plexiglass-like polymer, produced a material that could stretch over four times its size without fully breaking. In comparison, the polymer in other forms has little to no stretch and shatters easily once cracked.”
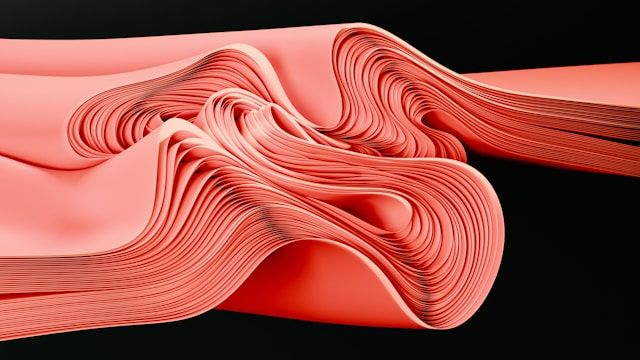
Significantly, the materials used as a starting point are merely standard industrial polymers. But when formed as metamaterials, they can be printed with exceptional strength and impact resistance but are much softer and more stretchable than their conventional polymer counterparts.
The study has now been published in the journal Nature Materials, where the team report on the remarkable improvement made through their approach to material design. Stating that, “double-network-inspired metamaterials by integrating monolithic truss (stiff) and woven (compliant) components into a metamaterial architecture, [can] achieves a tenfold increase in stiffness and stretchability compared to its pure counterparts.”
For years, research into metamaterials has focused on making extremely strong polymers, but has often ignored the advantages of softer, more pliable feedstocks.
“We’ve all been looking for the stiffest and strongest materials possible,” notes Prof. Carlos Portela, who led the study. “We realized that the field of metamaterials has not really tried to make an impact in the soft matter realm.”
By switching the search away from printing materials with struts and trusses, like those found in traditional lattice-based metamaterials, he and his colleagues moved towards creating an architecture of coils, or interconnected springs. This resulted in materials which were soft and springy, like rubber, even though the material they employed was actually hard, like plexiglass.
But this was not the final material the team had envisioned.
“They were stretchy, but too soft and compliant,” recalls Portela.

To resolve this issue, the researchers were inspired by hydrogels.
These soft, elastic, jelly-like substances, are primarily made of water with a small amount of polymer structure. For a long time, material scientists have been developing hydrogels that are robust, yet also soft and elastic. This they achieve by joining polymer networks with radically diverse characteristics, such as a naturally stiff molecular network which is then chemically cross-linked with another naturally soft molecular network.
“That was our ‘aha’ moment,” says Portela. “We thought: Can we get inspiration from these hydrogels to create a metamaterial with similar stiff and stretchy properties?”
By combining two different structures, a rigid scaffold of struts and trusses with a web of coils wrapped around each strut, the team were able to get the best properties from both designs.
They then printed out samples using acrylic plastic in a ‘high-precision, laser-based printing technique called two-photon lithography.’
“Think of this woven network as a mess of spaghetti tangled around a lattice,” says Portela. “As we break the monolithic lattice network, those broken parts come along for the ride, and now all this spaghetti gets entangled with the lattice pieces. That promotes more entanglement between woven fibers, which means you have more friction and more energy dissipation.”
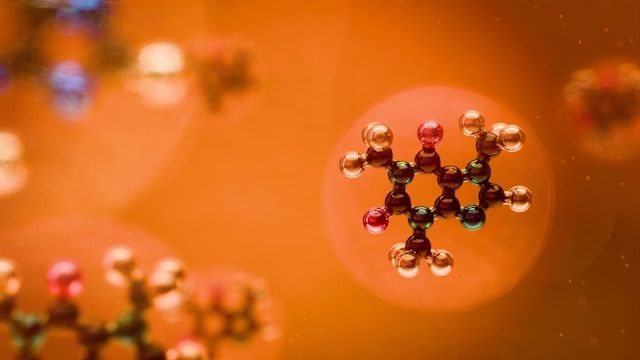
The results have been surprising, as the samples could be stretched three times their own length. That is ten times further than a traditional lattice-patterned metamaterial manufactured with the same acrylic plastic.
The team believe that this exceptional elasticity is based on the interaction between the coiled weave and the stiff struts of the new material when under stress and pull.
While the material’s design make look messy, it is the multiple knots and entanglements created spread across the stiff lattice which enables stress, stretching, or impact to be easily dispersed.
These properties are highly desirable in industry, and open up many possible applications, such as shock-absorbing components in aerospace, flexible yet durable clothing or wearable electronics, impact-resistant casings for electronics, or more flexible car body parts. Because the material's architecture allows energy to be dissipated efficiently without fracturing, it could also be vital in personal body armour, transport safety systems, and resilient construction materials.
Moreover, the compatibility of this design with 3D printing means that bespoke components could be produced on demand, tailored to specific mechanical requirements. For example, biomedical engineers could develop implants that adapt to movement inside the human body without degrading or losing strength over time.
Looking forward, the team is now investigating how to scale up the printing process and apply their double-network strategy to a wider range of substances, including metals, glass, ceramics, and composites.
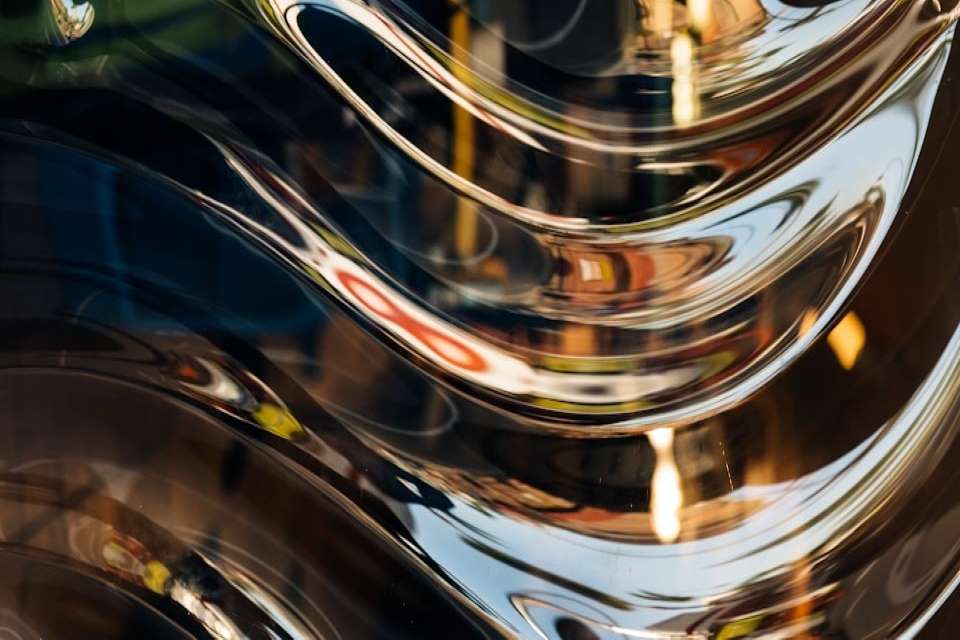
“We are opening up this new territory for metamaterials,” notes Portela. “We also want to try this approach on more brittle materials, to give them multifunctionality. So far, we’ve talked of mechanical properties, but what if we could also make them conductive, or responsive to temperature? For that, the two networks could be made from different polymers, that respond to temperature in different ways, so that a fabric can open its pores or become more compliant when it’s warm and can be more rigid when it’s cold. That’s something we can explore now.”
These innovations mark a profound shift in materials science—away from merely accepting the limitations of traditional substances and toward designing materials from the ground up with specific, tuneable properties.
By embracing nanoscale engineering and architectural ingenuity, manufacturers are no longer confined to the binary choice between strength and flexibility, rigidity and resilience, or durability and malleability. Instead, they can begin by defining what a product should do, set the properties needed for the feedstock, and allow nanomaterial researchers to design the raw material they need.
Photo credit: Paris Bilal on Unsplash, Tim Mossholder, Nina Cuk, Omar-Lopez Rincon, & Solen Feyissa