Nanotech Gives Polymer Adhesive Thermal Management
Nanomaterial application in polymers creates advanced materials for everyday manufacturing.
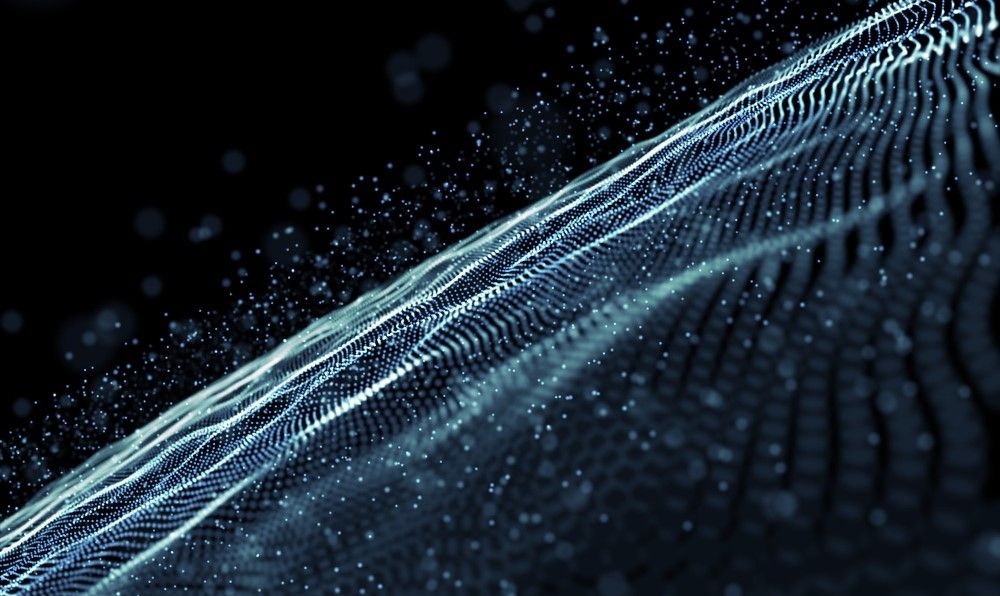
In modern manufacturing, there is a real need to supply materials which perform better, offer environmental neutrality, provide unique-selling points, or give other technical advantages over competitor products.
Where polymers are concerned, nanomaterials are meeting these needs and making a measurable impact across various segments of the manufacturing sector.
In the automotive industry, for example, nanoclays and carbon nanotubes are used to strengthen lightweight plastic parts without increasing weight. In plastic packaging, nano-silica and nanocellulose particles are improving barrier properties and extending shelf life while reducing the need for multilayer plastic films. In the coatings sector, nano-additives, like titanium dioxide and silver nanoparticles, are providing self-cleaning and antimicrobial properties. While modern construction materials now use nanocomposites to improve thermal insulation and flame retardancy.
These enhancements not only improve product performance but also help manufacturers meet environmental, safety, and durability standards.
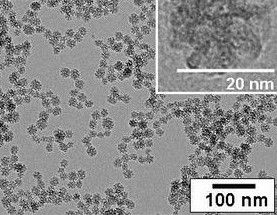
Another field of manufacturing that is constantly having to push the boundaries of technology is high-performance electronics. In this niche sector, overheating is more than an inconvenience—it’s a critical design bottleneck. And as devices get smaller, faster, and more powerful, effective thermal management remains a persistent challenge.
Yet here too, nanotechnology is providing solutions, as nanomaterial scientists have recently developed a new UV-curable adhesive reinforced with boron nitride nanosheets (BNNS) to provide heat management capabilities.
The breakthrough was made by creating a pressure-sensitive adhesive based on polyacrylate. Then when the researchers incorporated boron nitride nanosheets in an aligned, directional structure, they discovered that they had created a solvent-free material with high thermal conductivity which could maintain excellent electrical insulation and mechanical strength.
Boron nitride has long been known for its ability to conduct heat but not electricity, however, by examining its properties at the nanoscale, the researchers were able to innovate the way it is used to form a polymer adhesive with thermal management capabilities.
“By constructing a thermally conductive pathway through directional alignment of BNNS, we achieved a composite with a thermal conductivity of 0.96 W/m·K,” the study explains in the journal Polymers. This is a significant enhancement over traditional adhesives, which typically struggle to combine thermal management with electrical safety.
What makes this discovery stand out is not just the choice of material, but the method. The researchers manipulated the orientation of BNNS within the polymer matrix before curing it under UV light. This controlled alignment allows heat to move efficiently along the filler network—much like traffic flowing smoothly down a well-planned motorway—without compromising the adhesive's structural integrity.
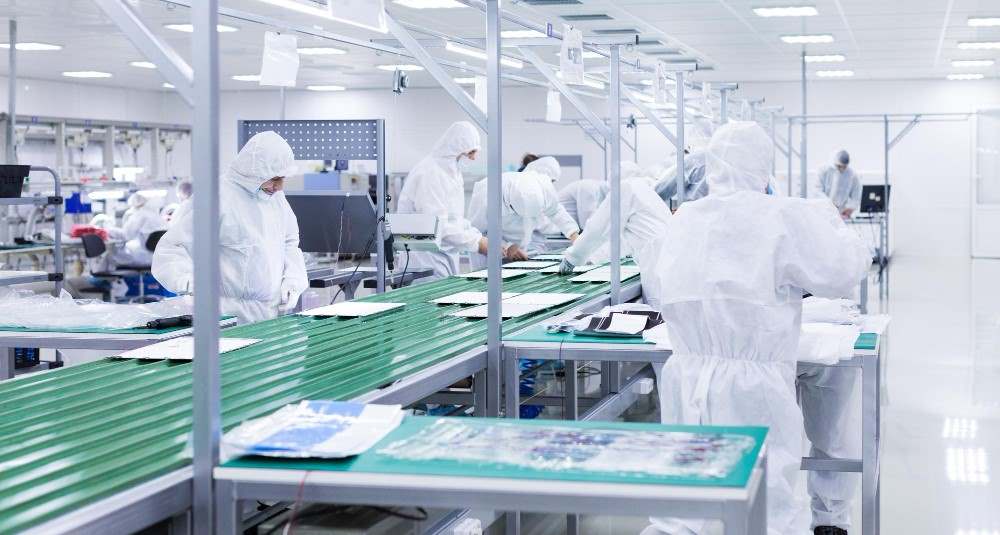
The electronics industry has long faced a trade-off: materials that conduct heat well often also conduct electricity—dangerous in delicate circuits—or they are too brittle to withstand mechanical stress. Thanks to nanotechnology, this new adhesive resolves that compromise.
“The composite showed excellent mechanical properties and electrical insulation along with enhanced thermal conductivity,” the study notes. That’s a powerful trifecta for designers of densely packed electronic components, such as those in 5G smartphones, EV battery packs, and LED modules.
Furthermore, the adhesive’s UV-curable, solvent-free composition offers major advantages for scalable, green manufacturing. It reduces volatile organic compound (VOC) emissions and supports energy-efficient processing. In an age of tightening environmental standards, this innovation hits multiple targets at once: performance, safety, and sustainability.
Related articles: Polyimide Films with Customised Thermal Performance or Nature’s Nanostructures Are Shaping Polymer Manufacturing
While the science behind the application of nanotechnology is complicated, the solution is actually quite simple.
BNNS are two-dimensional sheets (like graphene). They are electrically insulating and if left unorganised in a polymer, they don’t do much. But aligned properly, they create continuous pathways that allow heat to move with minimal resistance.
The team used a simple physical manipulation process to orient the nanosheets before curing. Once exposed to UV light, the polymer matrix quickly hardens, locking the aligned BNNS network in place. This approach eliminates the need for harsh chemicals or complicated processes, making it practical for commercial application.
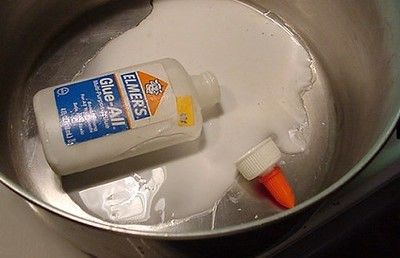
But this development isn’t just about lab results—it has real potential for industrial adoption. Solvent-free UV-curable adhesives are already widely used in electronics and medical devices. By incorporating nanotechnology into this existing infrastructure, the transition to high-performance thermal adhesives could be smooth and cost-effective.
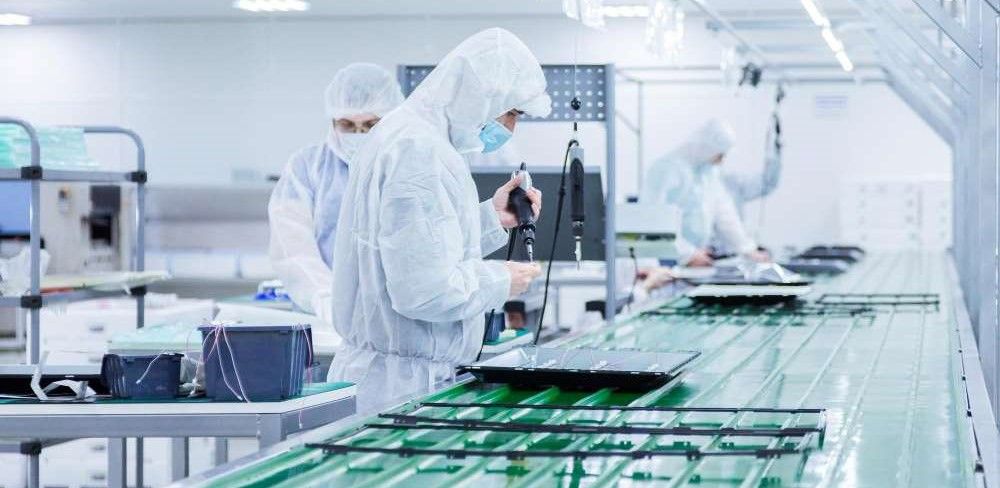
This new adhesive may not dominate headlines like artificial intelligence or quantum computing, but it’s a textbook example of how nanotechnology is transforming industrial materials from the inside out.
By fine-tuning the structure of matter at the nanoscale, researchers are solving problems that conventional materials have struggled with for decades. As this boron nitride innovation shows, nanotechnology isn’t only for futuristic breakthroughs; it’s about making everyday materials smarter, greener, and more competitive.
For manufacturers looking to stay ahead in demanding, high-performance sectors, the message is clear: the future of advanced materials is already here—just a few billionths of a metre at a time.
Photo credit: Flickr, usertrmk, Wallpaperflare, usertrmk on Freepik, kjpargeter, & Freeimages