Nanomaterial Design Improves Helmet Impact Resistance
Nanotechnology provides a new, lightweight, ultra-shock-absorbing foam that can help save soldiers’ lives.
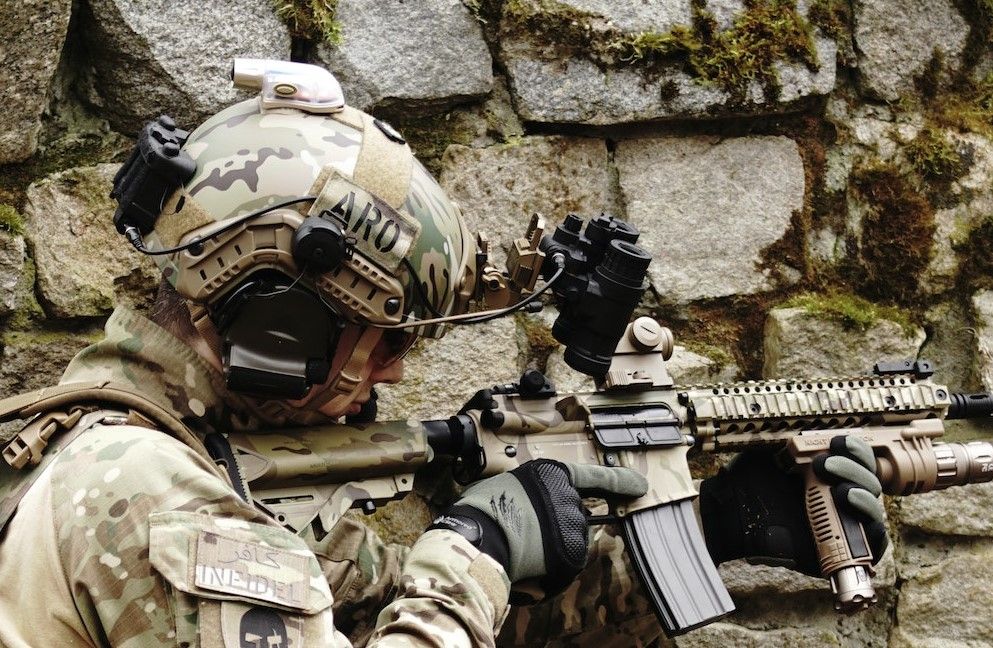
Nanotechnology researchers have made a breakthrough in raw material design which could save thousands of lives if applied to helmet construction.
The discovery, made at the University of Wisconsin–Madison involves using nanomaterials to create a lightweight, cushioning foam which has 18 times the specific energy absorption of foams currently used in U.S. military combat helmet liners. As well as softening the shock of any shrapnel, the new polymer composite also provides much greater rigidity and strength for further improved protection.
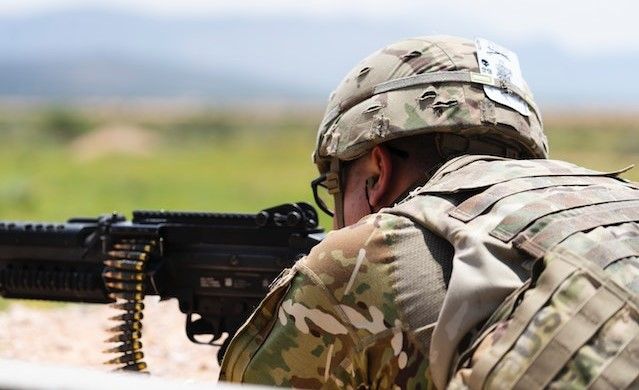
A concussion, permanent damage (such as loss of sight, memory, or hearing) and even death can be caused by the physical shock of an impact to the brain. A helmet which is more able to absorb or dissipate the energy of a blow to the head can lessen or even completely prevent such brain trauma.
“This new material holds tremendous potential for energy absorption and thus impact mitigation, which in turn should significantly lower the likelihood of brain injury,” explains Ramathasan Thevamaran, a UW–Madison professor of engineering physics and the research team’s lead.
The fundamental building blocks used by the researchers to construct the foam are carbon nanotubes – cylinders of carbon that are only one atom thick in each layer. By vertically orientating the carbon nanotubes into micrometre-scale cylindrical structures the foam provides extraordinary shock absorbing properties.
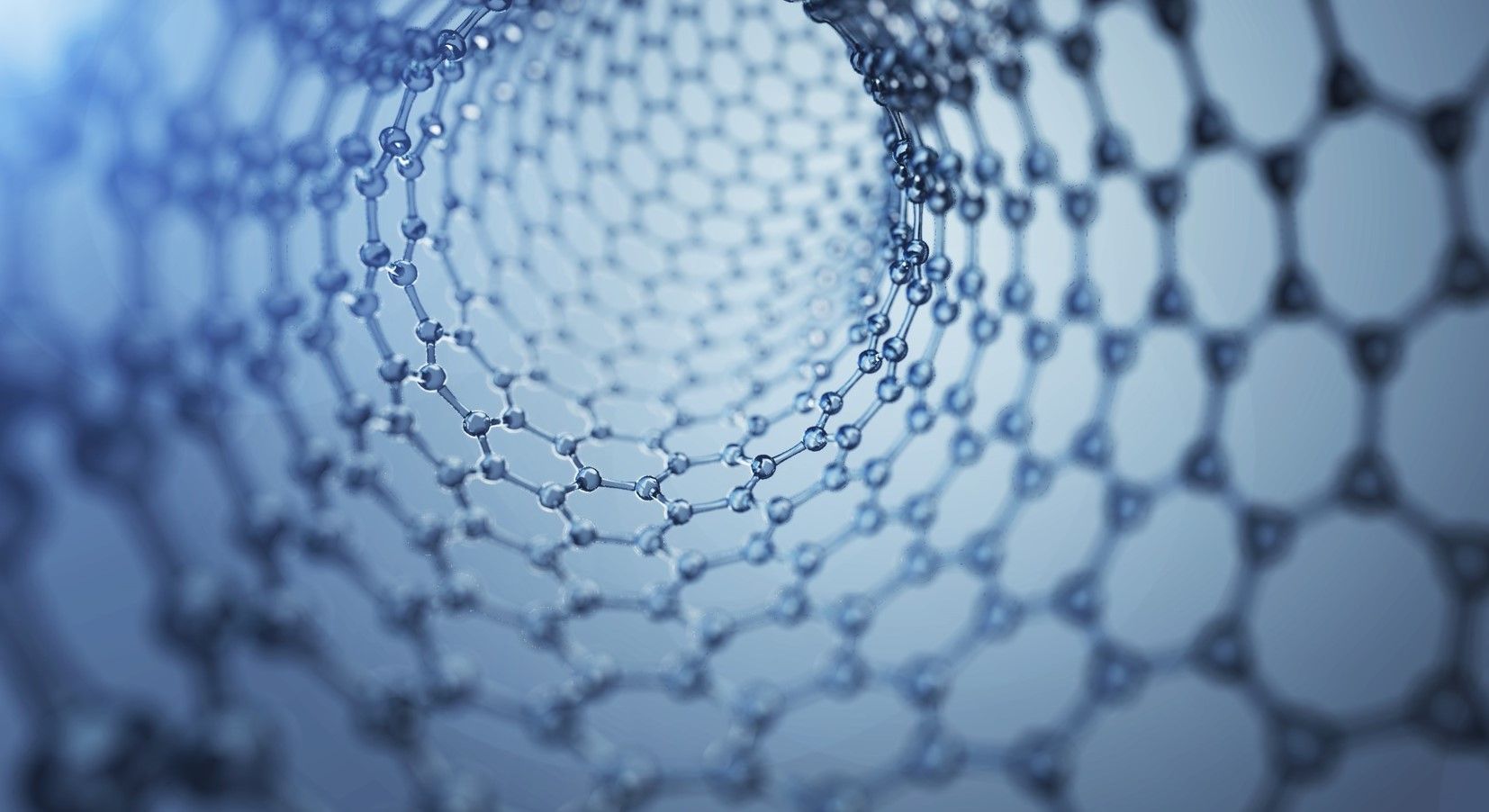
It was an arduous process to determine the new foam's ultimate optimal design criteria, which included cylinder thickness, inner diameter, and distance between adjacent cylinders. The experimentation was done methodically by the researchers, who adjusted each parameter and looked at every potential combination.
“We took a few different thicknesses, and then tested that with every diameter size and every possible gap, and so on,” says Thevamaran. “Altogether, we looked at 60 different combinations and conducted three tests on each sample, so 180 experiments went into this study.”
In doing so, the researchers found an obvious optimal size of cylinder - with a thickness of ten micrometres or less, closely aligned next to each other to provide a super-shock absorbing foam.
“I expected the overall properties to improve due to our interactive architecture, but I was surprised by how dramatically the properties were enhanced when the cylinders were 10 micrometers thick,” notes Thevamaran. “It was due to an unusual size effect that emerged in the process-structure-property relations. The effect was very pronounced, and it turned out to be quite advantageous for the properties we were targeting.”
Significantly, the foam remains effective in both very high and very low temperatures, making it a practical solution for helmet designs for a range of fighting environments.

However, the breakthrough is especially significant because it shows how nanomaterials are able to combine the best properties of dissimilar materials to overcome long-held challenges. As the researchers explain in their study published in the journal Extreme Mechanics Letters. “Protective applications in extreme environments demand materials with superior modulus, strength, and specific energy absorption (SEA) at lightweight. They must also have the ability to attenuate intense stress waves and absorb kinetic energy from impact while providing thermally stable functionality. However, these properties typically have a trade-off. Hierarchically architected materials—such as the architected vertically aligned carbon nanotube (VACNT) foams—offer the potential to overcome these trade-offs and achieve synergistic enhancement in mechanical properties…”
By designing better raw materials for use in helmets and other protective armour, nanomaterial engineers are showing how the world can be safer and manufacturing improved with the smart application of nanotechnology.
Photo credit: Matthew Hintz on Pexels, Specna Arms, Art Guzman, & FreePix