Lower Emission Plastics with Carbon Capture Nanotech
Carbon nanotubes as a raw material create polymers with a lower carbon footprint.
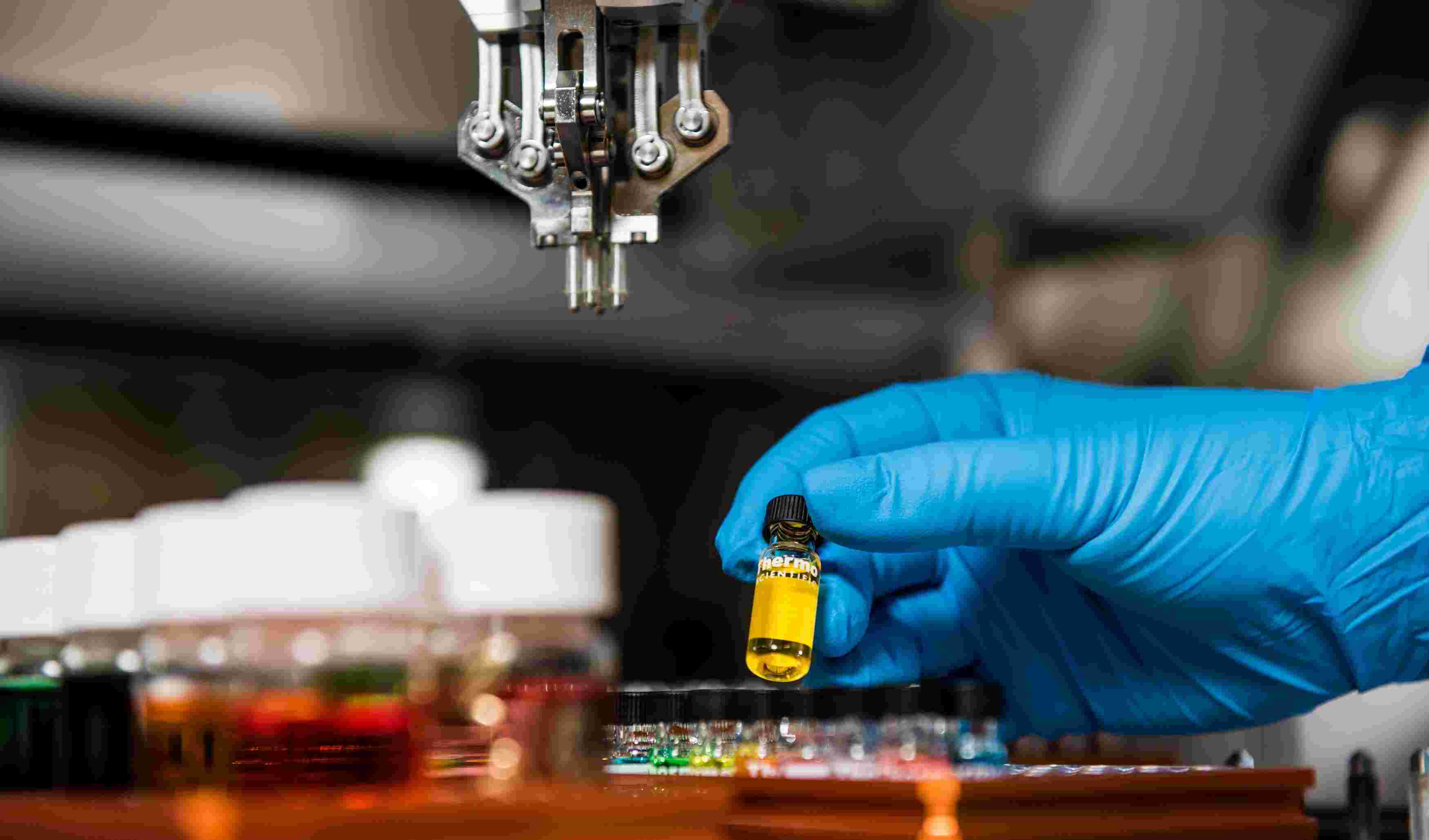
With the world's plastic consumption expected to double by 2040, there has never been a more pressing need to reduce the carbon emissions produced during polymer manufacturing.
One promising field of material research has looked into improving the quality of polymer feedstocks, so that less plastic is required to manufacture products. To achieve this, scientists have been studying carbon nanotubes (CNTs) – the strongest materials known to science – as a raw material which could help reduce the overall carbon footprint of plastics.
However, up until now, two major barriers have prevented CNTs from being widely used in plastic composites:
· the expensive cost of nanomaterial production.
· the energy-intensive nature of traditional CNT manufacturing techniques.
This impact is profound because the carbon footprint of producing nanomaterials contradicts the objective of making plastics that are more ecologically friendly.
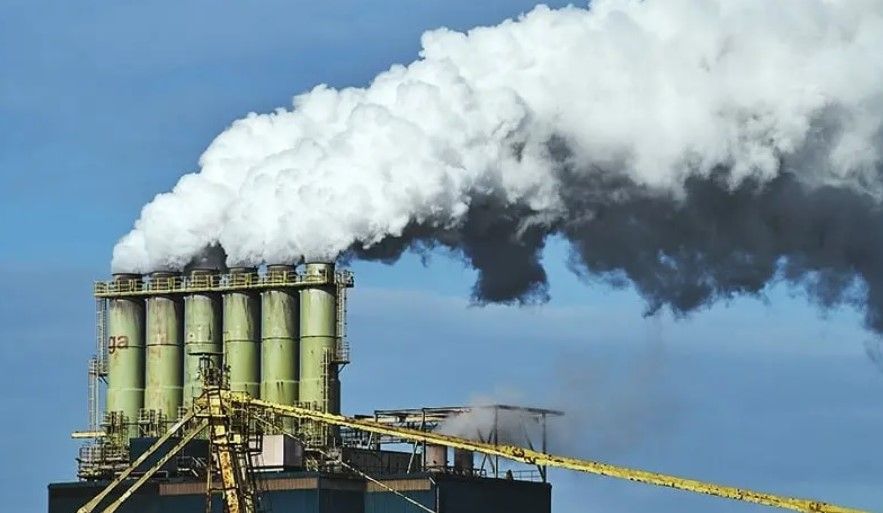
But now these obstacles may have been overcome by combining the technologies of carbon capture, CNT synthesis, and polymer science, to form stronger, more sustainable plastics with a reduced environmental impact.
As George Washington University’s Prof. Stuart Licht states, “Recent advancements in carbon capture and utilization technologies have opened up new possibilities for addressing these challenges.” Specifically, he reports how, “Our group and others have developed innovative methods to convert carbon dioxide (CO2) – the very greenhouse gas at the heart of climate change concerns – into valuable carbon nanomaterials, including CNTs. This approach not only provides a potential pathway for reducing atmospheric CO2 levels but also offers a more economical and environmentally friendly method for producing CNTs.”
The study, now published in the Royal Society of Chemistry’s journal Sustainability, describes the formation of, “carbon nanotube (CNT) lattices formed by carbon capture and utilization molten carbonate electrolysis of CO2.” The research goes on to explain how higher tensile strength polymer composites can then be made from the carbon capture CNTs, and that these composites use less polymer to achieve strength, thereby lowering the plastic product’s carbon footprint.
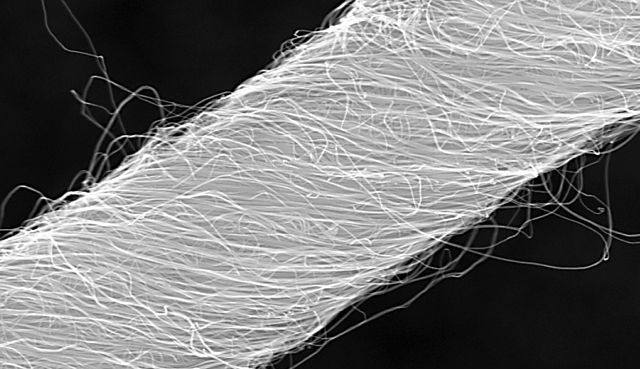
In a nutshell, a report in the industry journal Nanowerk outlines the process as follows:
“CO2 is dissolved in a molten carbonate salt and subjected to electrolysis, resulting in the formation of carbon nanomaterials at the cathode. The product of this process, termed a ‘carbanogel,’ consists of intertwined CNTs retaining some of the electrolyte within their structure. This carbanogel can be further refined to isolate the CNTs for use as additives in plastic composites.”
“We then investigated the effects of adding these CO2-derived CNTs to several types of epoxy resins and thermoplastics,” explains Licht. “We prepared composite samples with varying concentrations of CNTs and tested their mechanical properties, focusing particularly on tensile strength – a measure of how much force a material can withstand before breaking when stretched.”
The results of these tests were impressive, with the addition of only 1.5% by weight of CNTs in a deep-pour epoxy resin called Timber Cast resulting in a 30% increase in tensile strength compared to tests conducted on the resin alone. Logically, the amount of resin could then be reduced by almost a third (lowering the product’s carbon footprint) if CNTs were added.
Similar tests conducted on a thin-coat epoxy called Varathane and a fast-curing epoxy known as Jetset-Metlab also showed greatly increased tensile strength when equally low quantities of nanomaterials were added. Other experiments measuring hardness, also found improvements through the inclusion of CNTs.
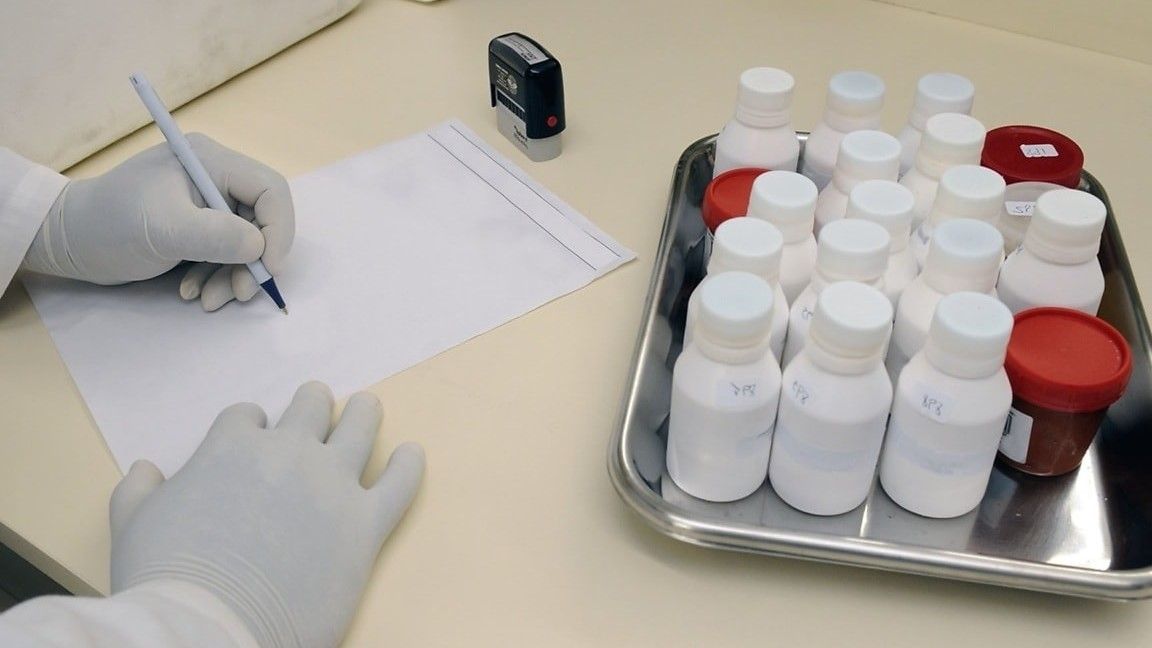
From a business angle, the CO2-to-CNT method could considerably lower the cost of creating carbon nanomaterials. And while full analysis of the economics has yet to be conducted, early predictions indicate that the electrolysis-based approach could reduce carbon nanomaterial prices to about $1000 per tonne as opposed to conventional chemical vapour deposition methods which mass produce CNTs at about $1 million per tonne.
But it is the environmental angle that most impresses Licht and his team.
"Our work represents a significant step forward in the quest for more sustainable plastics,” he states. Noting that, “As this technology continues to develop, it could play a crucial role in reducing the environmental footprint of plastics while maintaining or even enhancing their performance characteristics.”
Through the strategic deployment of advanced nanomaterials, the very emissions that have long plagued the production of plastics can now be harnessed and sequestered, preventing them from contributing to climate change. It is a technological renaissance that promises to rewrite the narrative of plastic's environmental impact, transforming a once-maligned industry into a core role of sustainable innovation.
“The implications of our findings are quite significant,” says Licht. “By enhancing the strength and other properties of plastics, CNT additives could allow for the use of less material to achieve the same performance characteristics. This reduction in material use could translate directly into a lower carbon footprint for plastic products. Moreover, the use of CO2 as a feedstock for producing the CNTs adds an additional layer of environmental benefit, potentially turning a greenhouse gas into a valuable material resource.”
For it now seems that combining carbon capture and nanomaterial science has formed a pathway to making stronger plastics, while at the same time reducing carbon emissions.
If you would like to know more about how carbon nanomaterials can improve polymer products, such as epoxy resins or polycarbonate granules, then visit POLYMER NANO CENTRUM - an innovative Czech company focused on the application of nanotechnology in polymers.
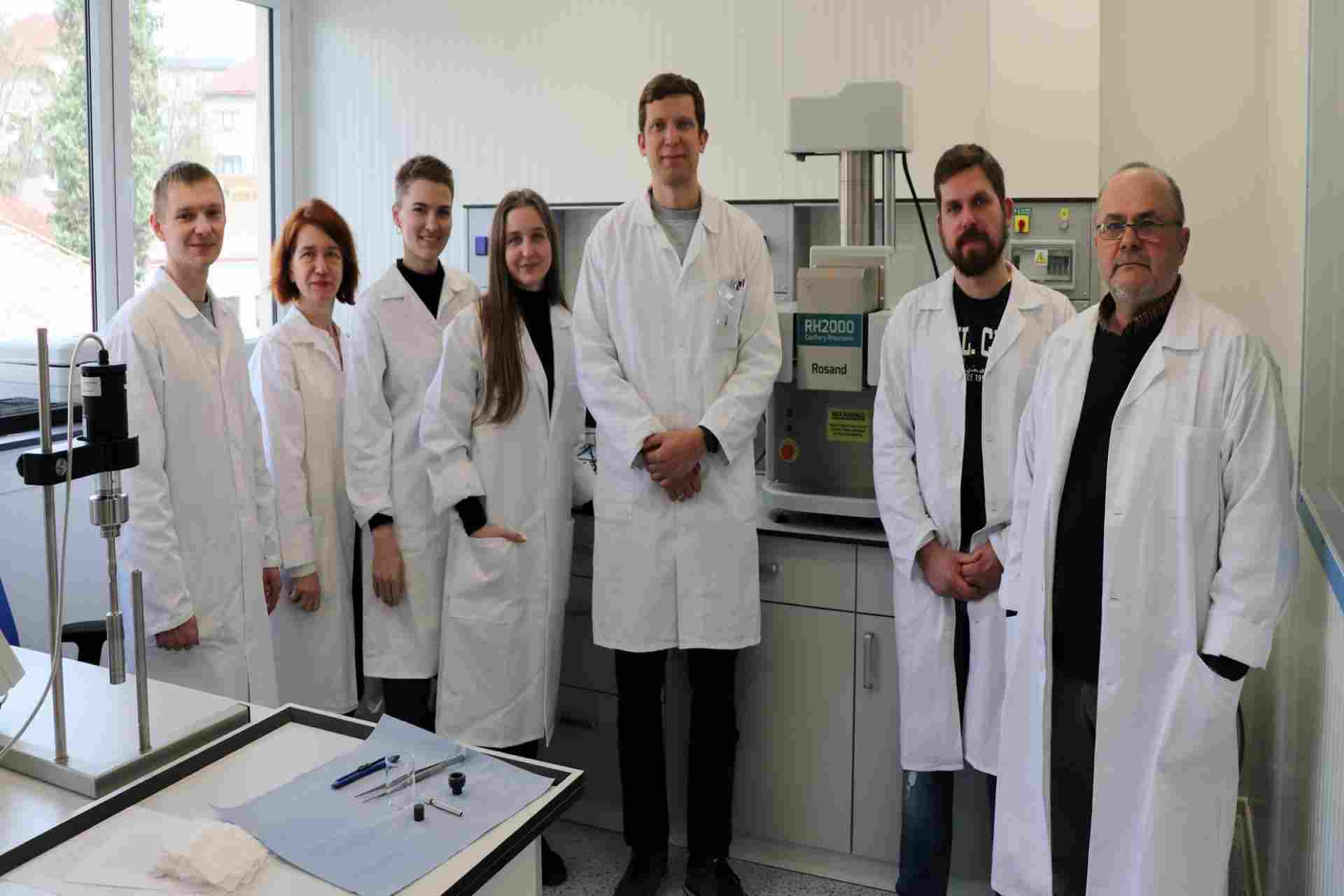
POLYMER NANO CENTRUM (who sponsor this webpage) have years of experience in developing unique nanostructuring technologies suitable for industry.
Photo credit: Wikimedia, PolymerNanoCentrum, Pixnio, Freemalaysia, & Rawpixel