How 3D Printing and Nanotechnology Improve Body Armour
Additive manufacturing is now a key tool to making stronger, lighter, and more protective bullet-proof clothing.
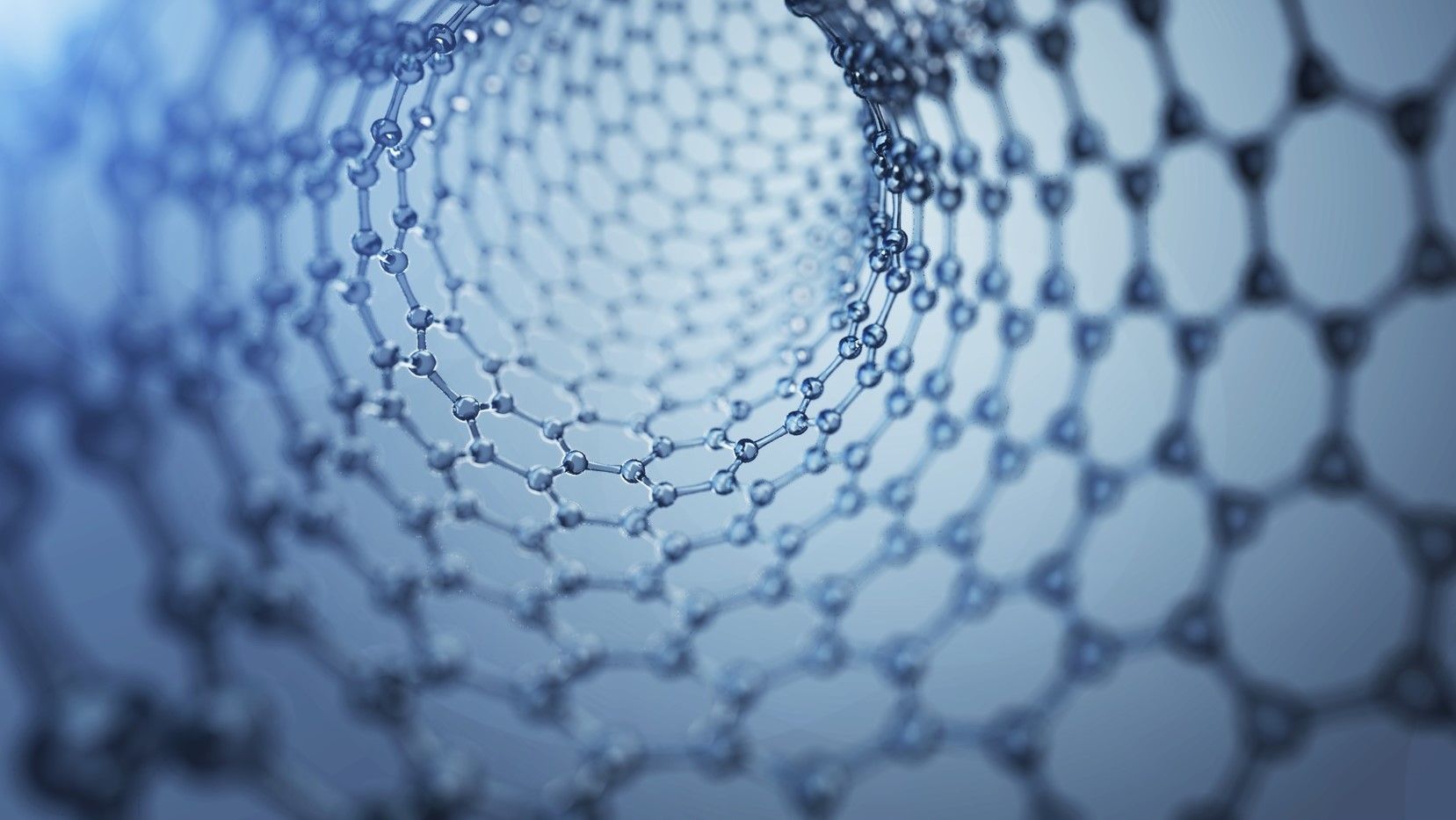
During the American War of Independence British soldiers were expected to carry 36 kilos of equipment during a march. By the Gulf War this load had increased to 45 kilos. As modern military equipment possibilities grow (more powerful guns, anti-tank and anti-aircraft weapons, mortars, RPGs, etc.) so does the burden on the modern soldier.
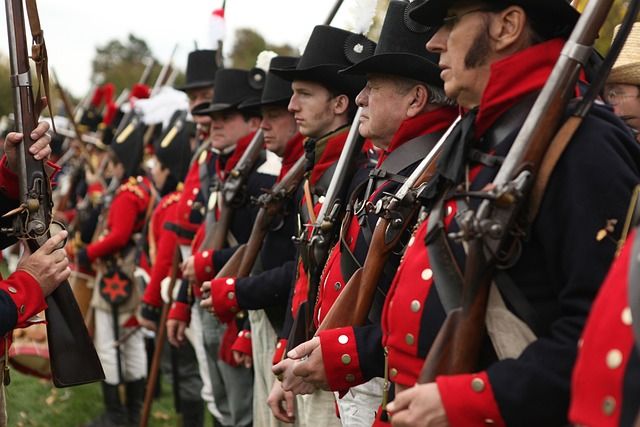
With body armour and modern helmets now an essential part of combat clothing, even without full kit, a soldier is heavily laden when on the battlefront.
Modern military hardware design is now heavily focused on lightening the load that a soldier has to carry – and 3D printing (additive manufacturing) and nanomaterials are at the heart of achieving this goal. Here's why:
1. Flexibility of Design
With additive manufacturing, more complicated designs can be created than if using conventional manufacturing techniques. With the use of 3D printing, design limitations that are present in more conventional procedures are no longer an issue.
2. Nanomaterials
With their superb strength and low weight, nanomaterials are an ideal raw material for use in additive manufacturing.
For example, due to their large surface area to weight ratio, carbon nanotubes (the strongest material known to science) can impart their strength into a composite largely made up of conventional raw materials. By reducing the quantity of raw material input, overall weight is reduced at the same time as costs are lowered making this technology widely used in making super-tough composites for use in the aviation and automobile industries.
To learn more about this topic read: Carbon Nanotubes Create Cheaper Production of Strong Composites.
For military purposes, nanotechnology can provide a polymer used in body armour with improved impact protection that works in extremes of hot and cold while still providing excellent resistance to scratching and cracking.
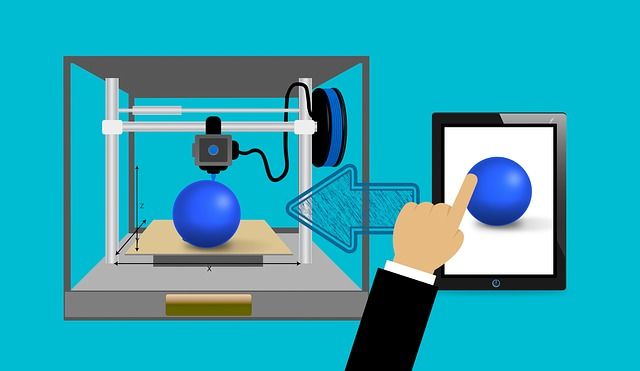
3. Print on Demand and at the Battlefield
Another benefit of additive manufacturing is that, unlike traditional production methods, it doesn't require much space to store inventory. As there is no need to print in quantity unless necessary repairs can be made remarkably close to the battlefront.
Since the 3D design files are printed using a 3D model as either a CAD or STL file, they are all kept in a virtual library where they can be accessed and printed as needed. By altering individual files, changes to designs can be made for relatively low cost without wasting outdated stock or spending money on tools.
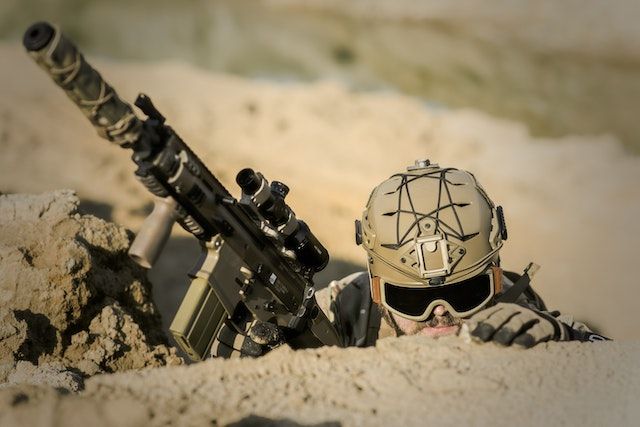
4. Faster Production Set Up
Compared to moulded or machined parts, 3D printing can produce an object in a matter of hours, depending on the part's complexity and design. Through 3D printing, time can be saved not only during the part's production but also during the design phase by producing STL or CAD files that are ready for printing.
5. Rapid Prototyping
The prototyping process can also be sped up by 3D printing’s ability to produce parts in a matter of hours. This makes it possible for each step to finish sooner. In comparison to machining prototypes, 3D printing is less expensive and faster at producing components, which in turn makes it possible to complete each design alteration much quicker.
6. Cost Efficiency
Because 3D printing is a one-step manufacturing method, it reduces the time and expenses involved when compared to the conventional use of machinery for production. There is also no requirement for operators to be present at all times when using 3D printers; they can be set up and allowed to complete the task.
7. Stronger and Lighter Parts
Although some metals can also be used in additive manufacturing, plastic is the primary raw material. As well as being innately much lighter than their metal counterparts, plastics are an ideal solution for honeycomb designs.
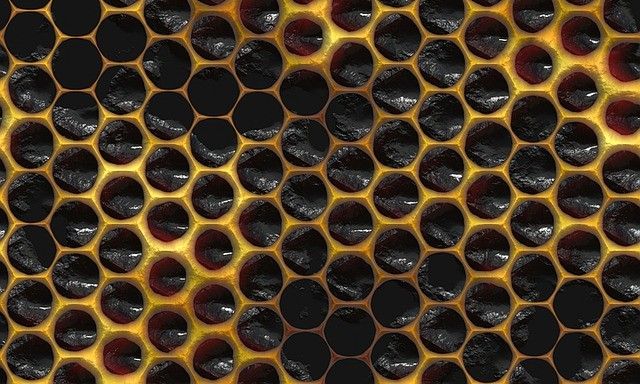
Additionally, pieces can be made from customized composites (such as those containing nanomaterials) to offer particular qualities like heat resistance, increased strength, water repellency, or impact protection.
8. Minimal Waste
When compared to other technologies, which use enormous chunks of non-recyclable materials, additive manufacturing creates components from materials required exactly for the part itself, with little to no waste. The procedure not only conserves resources, but also lowers feedstock input costs.
9. Environmentally Friendly
By nature, additive manufacturing aids progress towards NetZero because it decreases the quantity of raw material waste. When also considering increased fuel efficiency from using lightweight 3D printed parts, the environmental advantages are clear.
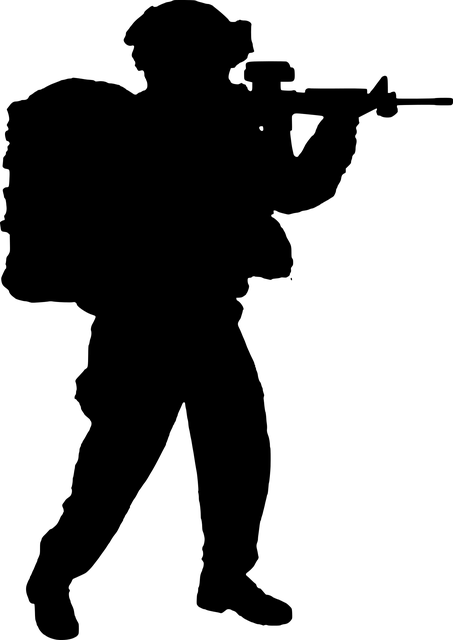
While the list of the advantages of 3D printing is not endless, each point remains a persuasive argument for changing manufacturing processes away from more conventional methods.
The ability to reduce raw material waste, the application of nanotechnology, the possibility of producing or repairing close to the battlefront are practical solutions that can outweigh the initial cost disadvantage.
With the ongoing conflict in Ukraine costing many lives daily, the need to improve body armour design has become paramount. 3D printing and the smart application of nanomaterials are key to winning that and any future conflict.
Photo credit: Pete Linforth form Pixabay, Mohammed Hassan, Spencer, Mohammed Hassan, Pixabay, & Freepik