A Breakthrough in Polymer Nanocomposite Manufacturing
How a one step, dual stage monitoring system will push polymer composite production and control to the next level.
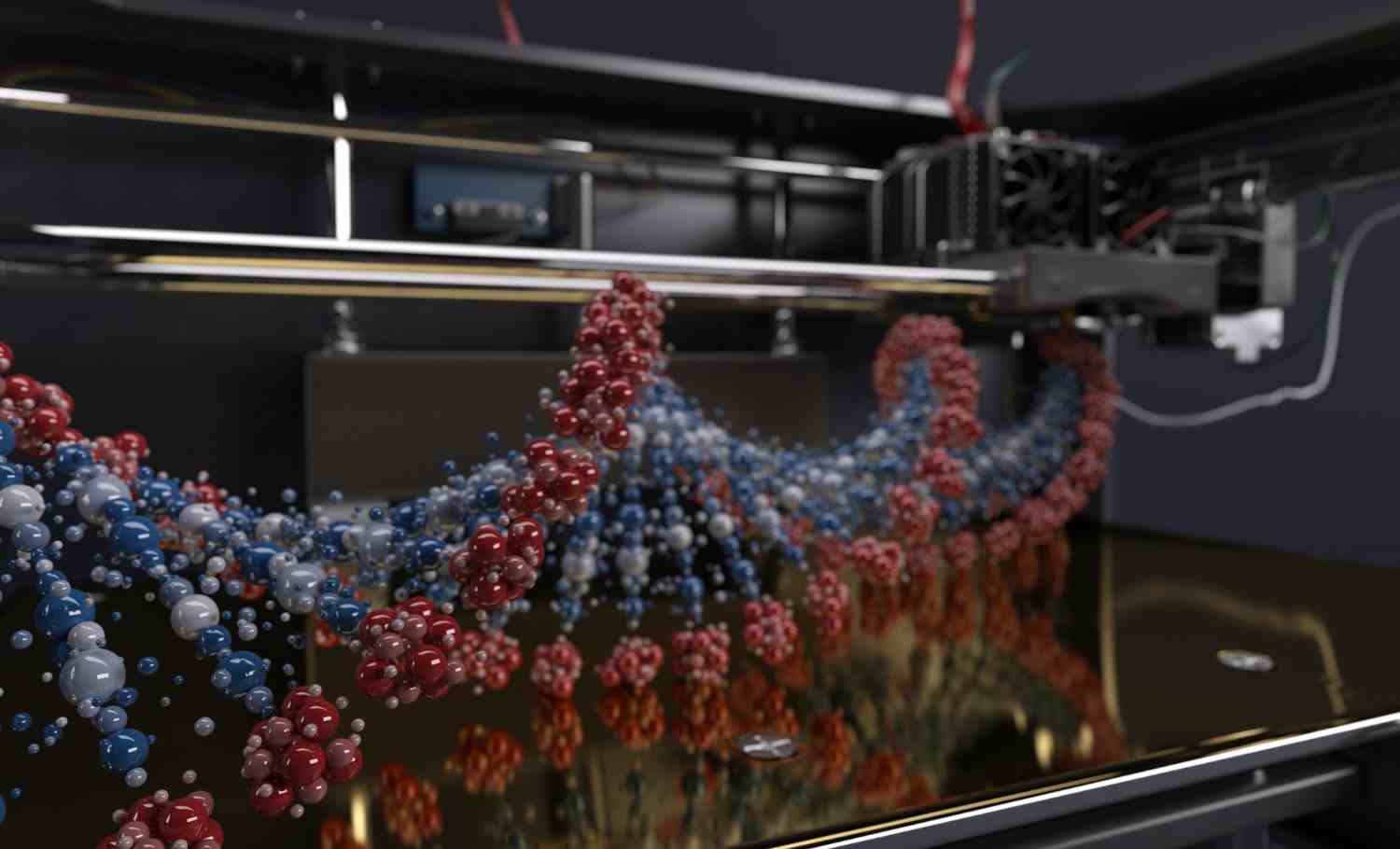
In the race to create smarter, more resilient polymer nanocomposites, one challenge has persisted: how do we monitor structural performance throughout the material’s entire lifecycle—from production to final use—without compromising its integrity?
Now a recent breakthrough by researchers at Skolkovo Institute of Science and Technology (Skoltech) may offer a powerful answer. By embedding conductive carbon nanotube fibres (CNTFs) directly into the polymer matrix, they’ve developed a simple, scalable technique that allows for dual-stage monitoring—capturing data both during manufacturing and in long-term service. It is a discovery which could redefine how nanocomposite materials are produced, qualified, and maintained.
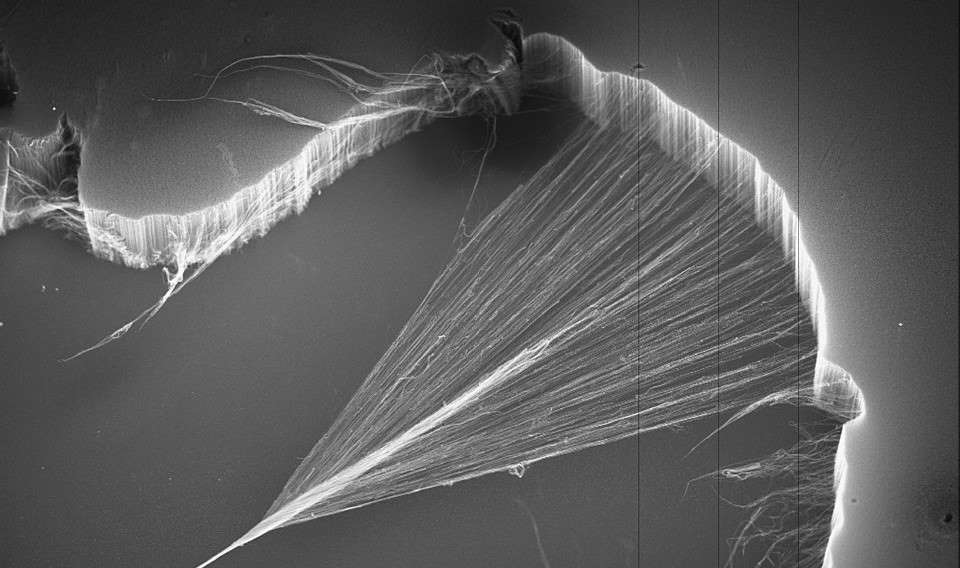
Traditional monitoring approaches in polymer composites are typically separated into two stages: production quality control and in-service structural health monitoring. Each relies on different tools and setups.
During manufacturing, sensors may track temperature, pressure, or curing behaviour. Once deployed in the field, composites often require embedded strain gauges or external sensors to monitor usage-related stress or damage.
However, this two-system approach introduces inefficiencies and often affects the material’s mechanical properties. Additional interlayers, adhesives, or invasive electronics can compromise composite integrity. For this reason, the polymer industry has long sought a unified, non-invasive solution that can function throughout the material’s lifespan.
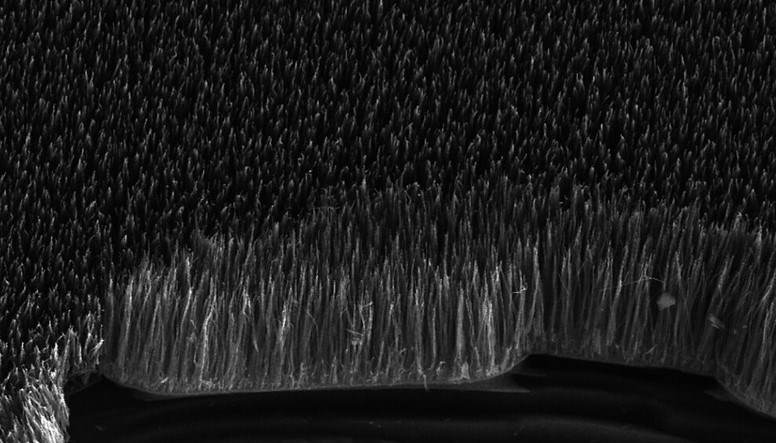
Skoltech researchers, led by Yury Nasibulin and colleagues from the Laboratory of Nanomaterials and Advanced Composites, tackled this challenge using thin, conductive filaments made of aligned single-walled carbon nanotubes.
“I believe old monitoring techniques, such as interlayers and embedded devices, have just lost a significant part of their relevance,” explains Assistant Professor Dmitry Krasnikov, who worked on the study. “The idea behind the work was to design a materials-based monitoring technique, which prepares the field for upcoming industrial products.”
The study, which has now been published in the journal Carbon, explains how the simple application of this nanotechnology has resolved the issue. Explaining how, “Carbon nanotube fibers (CNTFs) were embedded into the nanocomposites during their manufacturing to monitor changes (1st stage), and were left embedded to also monitor their lifecycle (2nd stage).”
Because CNTFs are both mechanically robust and highly conductive, they serve as internal sensing elements. They can register subtle changes in electrical resistance that correspond to mechanical deformation or structural damage. Importantly, they do this without weakening the material or adding bulk, making them ideal for embedded use.
This setup allows for real-time data collection during fabrication—such as resin flow or curing behaviour—and continues to function during long-term use, providing early warnings of fatigue, cracking, or overstrain.
Related articles: Nanotech Gives Polymer Adhesive Thermal Management and Nature’s Nanostructures Are Shaping Polymer Manufacturing
Notably, the sensor integration required no adhesive layers, protective coatings, or mechanical interfaces—just direct contact between the CNTFs and polymer resin, with no compromise in tensile strength, modulus, or fracture resistance.
“By simply placing carbon nanotube fibers (CNTFs) into the nanocomposites during their manufacturing, we are able to monitor the entire production process and variables,” says Krasnikov. “The CNTFs don't need to be removed since they cause no change in mechanical performance and can be utilized to provide information on material damage, strain, and a host of other factors during their service life.”
Why This Matters for the Polymer Industry
This technique offers multiple benefits for composite manufacturers and end users alike. These include:
· Seamless monitoring during and after fabrication
· Improved product reliability, thanks to early detection of faults
· Elimination of bulky external sensors or destructive testing
· Lightweight, scalable approach compatible with existing production methods
This has serious implications for industries such as aerospace, automotive, wind energy, and infrastructure, where structural health monitoring is critical and material failure carries high costs.
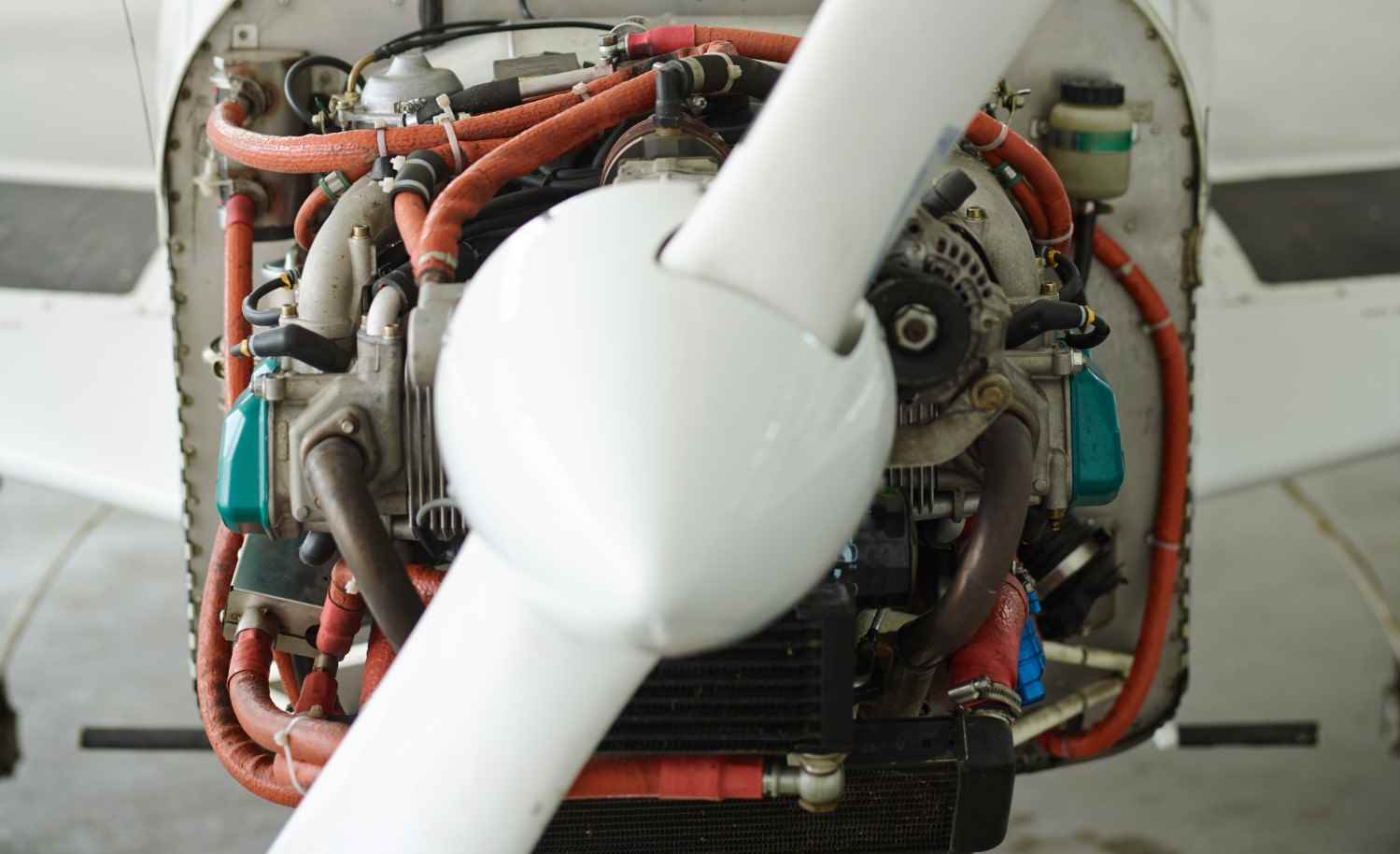
Furthermore, while the current work focuses on passive electrical resistance monitoring, the approach could be expanded further in the future. For example, integration with wireless telemetry, AI-driven damage detection, and even multi-material sensor arrays are already on the horizon. Skoltech’s scalable synthesis of CNTFs also supports adaptation to other nanomaterials, including graphene and MXenes.
With this dual-stage CNTF-based monitoring method, Skoltech researchers have introduced a powerful new tool for the polymer nanocomposite community. It combines simplicity, reliability, and versatility—addressing long-standing gaps in manufacturing control and structural diagnostics.
“Advanced composite monitoring currently relies on techniques which are either specialized for material manufacturing or application stages,” notes the study’s lead author, Hassaan Ahmad Butt. “They are often not interchangeable, and we wanted to essentially positively disrupt the way things are done for nanocomposites.”
As such, this is more than just a monitoring technique—it's a step towards truly intelligent nanocomposites, capable of communicating their own health status in real-time.
Photo credit: Wikimedia, Flickr, Pressfoto on Freepik, & kjpargeter