3D Printed Nanomaterials Boost Bullet-Proofing
Better than Kevlar, twice as strong as steel; a combination of nanotechnology and 3D printing has provided a body armour breakthrough.
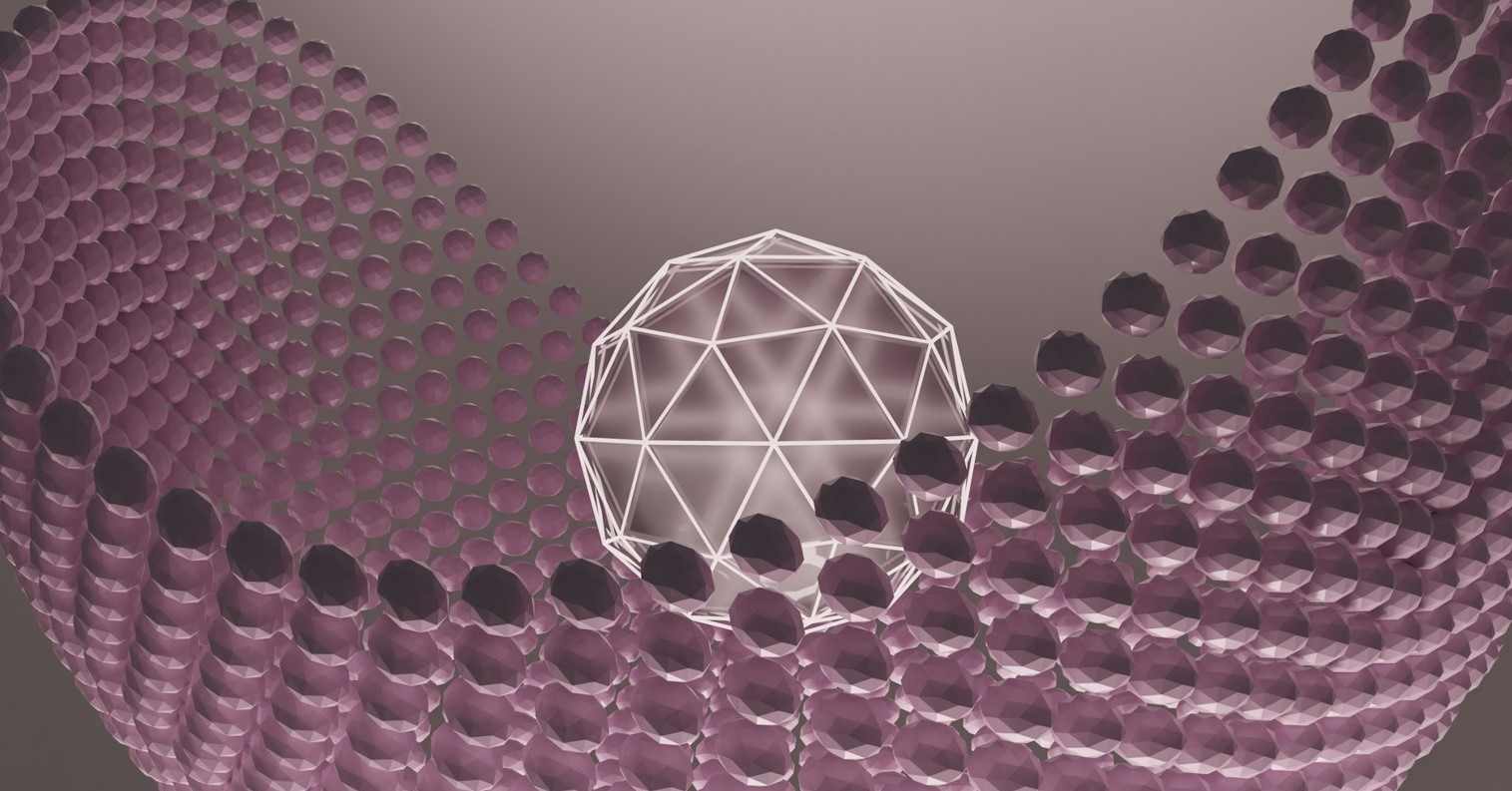
What could be a more logical feedstock for improving personal body armour than nanomaterials? Their combination of flexibility, exceptional strength, and low weight make them an ideal raw material for manufacturing bulletproof vests and blast protective armour.
Working on this idea, a team of researchers from MIT, Caltech, ETH Zurich and the US Army Research Lab have collaborated to devise a process which uses a fourteen sided 3D shape called a tetrakaidecahedron to take nanomaterial inclusion in body armour to the next level.
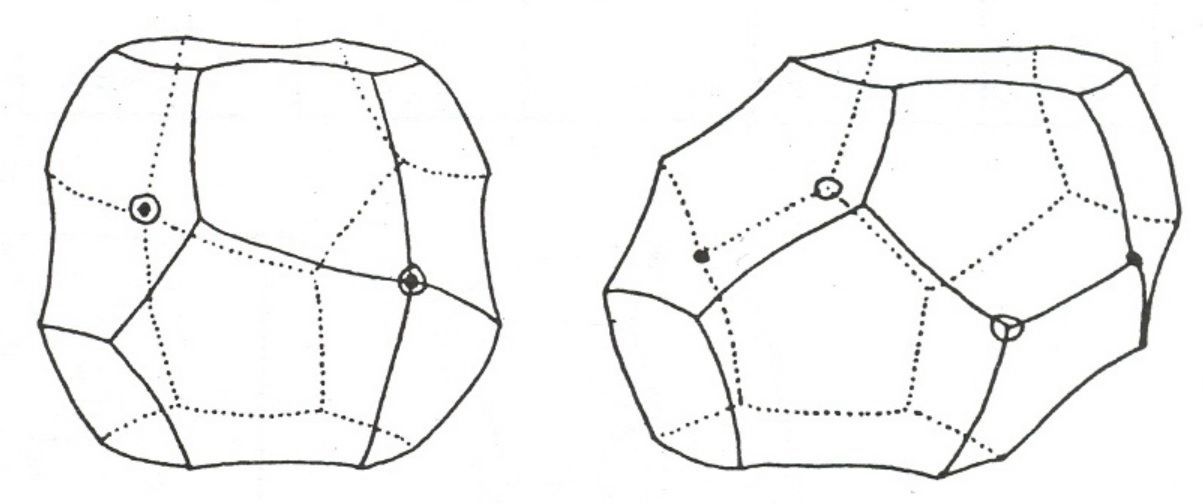
The tetrakaidecahedron structure was first theoretically suggested in the 1800s as one of the most efficient structures for occupying space with copies of itself. “Historically, this geometry appears in energy-mitigating foams,” notes Asst. Prof. Carlos Portela, the study’s lead author.
Up until now, these materials have only been studied in depth for their load-bearing strength, but now their full potential for absorbing impact has also been analysed with ground-breaking results for the body armour industry.
In fact, if the study’s findings are correct, then the novel nano-architected material has the potential to replace Kevlar in a variety of bulletproof protective gear and blast-proof armour.
“This work could provide design principles for ultra-lightweight impact-resistant materials for use in efficient armor materials, protective coating, and blast-resistant shields desirable in defense and space applications,” notes Cal Tech’s Prof. Julia Greer, who led the study.
Nanomaterials are miniscule, measuring smaller than 10,000th the width of a human hair. At this scale, materials take on new properties, for example becoming exceptionally strong without a huge increase in weight. Nanomaterial researchers are also able to modify nanomaterials to further improve impact strength, flexibility, or other characteristic.
The tetrakaidecahedron nanomaterial starts as a special light-sensitive substance that changes shape when exposed to a laser light process called two-photon lithography. A precise laser moves through this substance in 3D, hardening it layer by layer to create the desired structure. Once the structure is fully formed, it is heated to a high temperature in a furnace, which burns away parts of the material and transforms the polymer into a strong, carbon-based material called pyrolytic carbon.
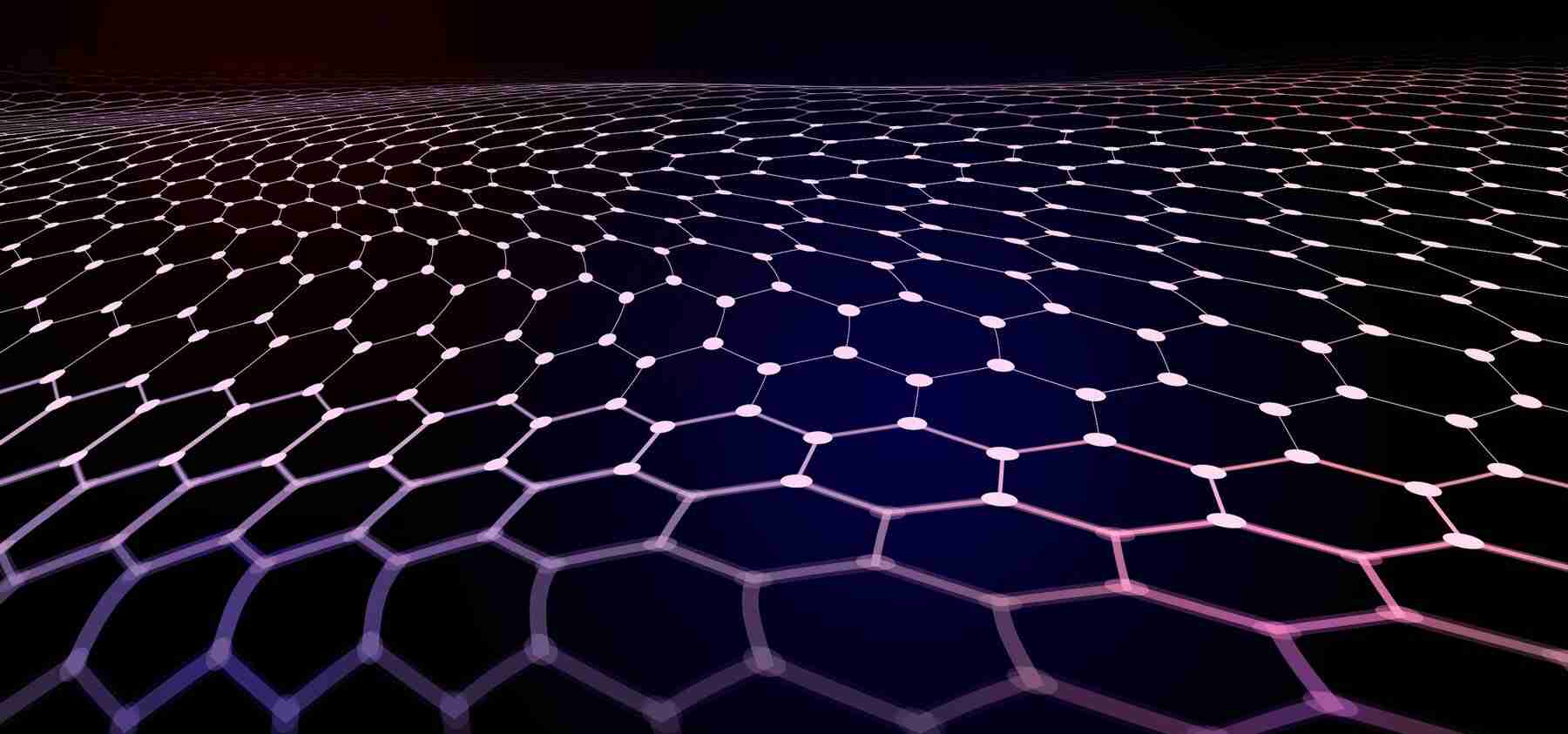
It is this nano-structured material that was tested for impact strength, as the industry journal 3D Printing Industry explains, “Two versions of the ultra-thin material were created with different densities and blasted with microparticles of 14-micron diameters at speeds of between 40 and 1,100 meters per second. For reference, the speed of sound is 340 meters per second. The denser version of the material was found to be more resilient to the blasts, with the microparticles embedding themselves in the material rather than tearing through, as would be the case with either fully dense polymers or carbon sheets of the same thickness.” Adding that, “The carbon struts immediately surrounding the microparticle were observed to crumple while the overall structure remained intact.”
Related articles: DIY Nanomaterial-Based Body Armour or Medieval Chainmail Inspires Next-Generation Body Armour
The study has now been published in the journal Nature Materials, where the researchers state that, “… the material can absorb a lot of energy because of this shock compaction mechanism of struts at the nanoscale versus something that’s fully dense and monolithic, not nano-architected.”
Incredibly, the nanomaterial performed twice as well in the impact tests than steel, and 70% better than Kevlar composites. Not only does the 3D printed nanomaterial have superb impact strength, but it is also very flexible, making it an ideal raw material for body armour.
“While carbon is normally brittle,” says Portela, “the arrangement and small sizes of the struts in the nano-architected material gives rise to a rubbery, bending-dominated architecture.”
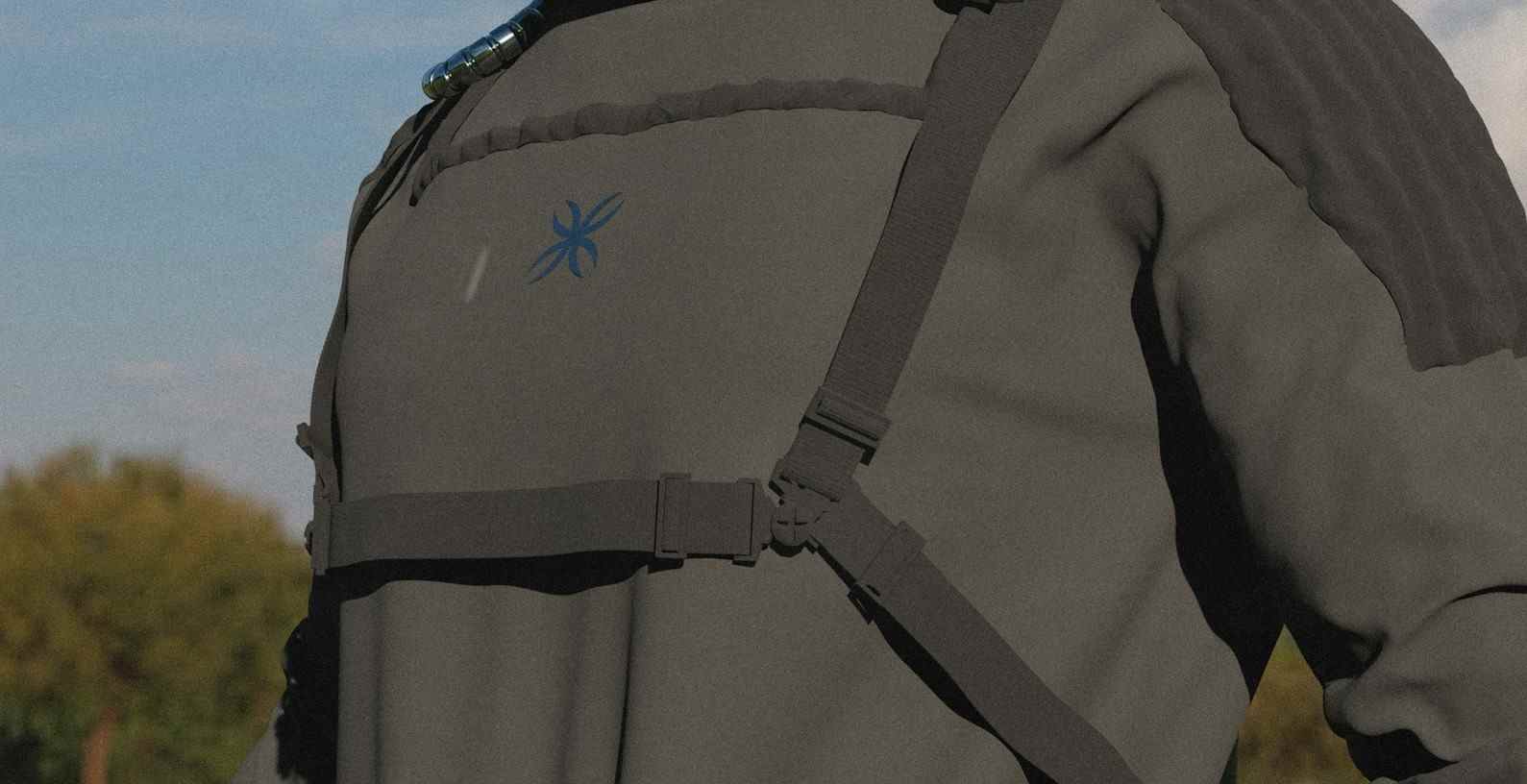
Looking ahead, the researchers believe that the nano-structured carbon will be ideal for use in military personnel armour, protective coatings, impact shields for spacecraft, and blast-resistant helmets, although they do acknowledge that further development is required before the material may be used in real-world applications or upscaled to an industrial process.
Meanwhile, research is ongoing on this and other nanomaterials to see how well they can withstand similar high-speed impacts.
The development of this 3D-printed nanomaterial marks a significant leap forward in protective armour technology—an innovation which could revolutionize defence, law enforcement, and other industries that rely on impact-resistant materials. As research progresses, nanomaterial breakthroughs like this bring industry closer to manufacturing next-generation armour that is both stronger and more efficient than ever before.
Photo credit: Freepik, Wikipedia, Rootnot creations on Unsplash, & Pallab Kumar Nakti