Nanomaterials for Better Impact Protection
MIT researchers are utilising nanotechnology to help create body armour that is both tougher and lighter.
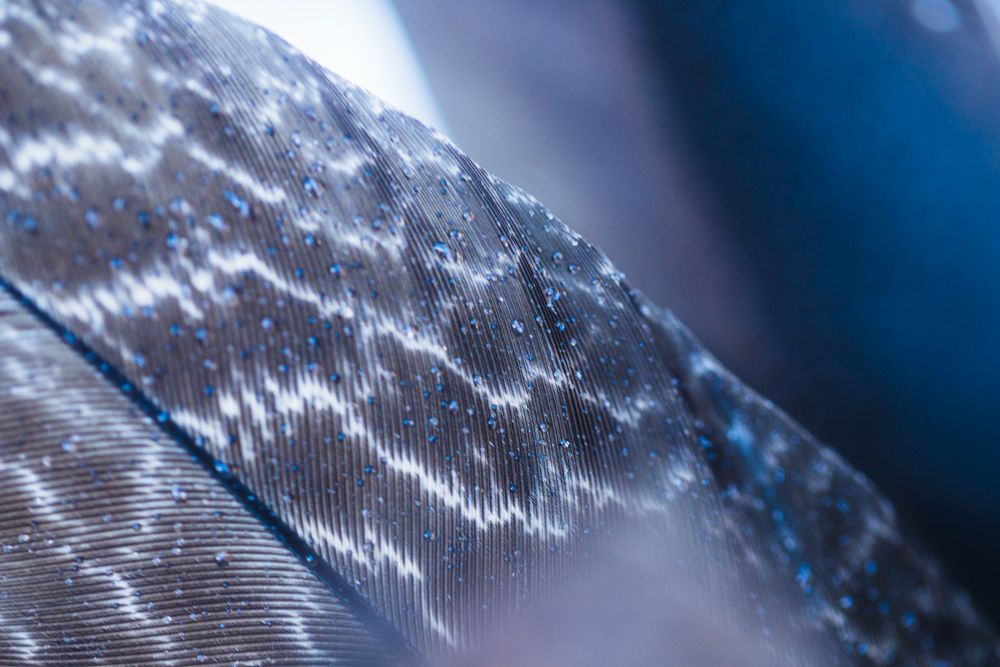
Researchers at MIT's Soldier Institute for Nanotechnologies have developed a technique that allows them to improve polymers with nanomaterials to make novel composites ideal for personal body armour and helmets.
Currently, most personal protective gear is made from Kevlar, a well-known brand of material designed for its strength and resistance to penetration. However, this raw material has significant disadvantages, such as poor compressive strength and sensitivity to environmental factors.
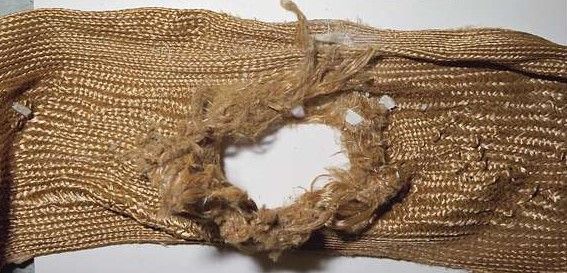
To avoid these drawbacks, material scientists have gone back to basics and are analysing how materials gain properties at the smallest scale – the nanoscale.
Through an improved understanding of nanomaterials, today’s scientists are able to build substances ‘from the bottom up’ to create materials which at their earliest creation have energy dissipating properties.
Doing so has allowed for the design and then manufacture of materials which have unusual forms but also very novel properties. These include exceptional stiffness and strength, but also extremely low weight.
“You start off with a substrate,” explains Carlos M. Portela, a researchers at MIT’s Department of Mechanical Engineering. “Which, in our case, is just a silicon chip, and then you put a drop of a photo resist or your resin, and then this laser, you can actually tightly focus it at a very small nanoscale spot, and wherever this spot gets traced, you locally solidify it.”
While the nanotechnology is complex, the overall design for the protective armour is incredibly simple, as Todd South, a reporter at Military Times, outlines.
“[A motorcycle] helmet has a protective shell. It protects the rider if they crash or bump their head in any way, but it basically has one or two layers of protection. That's kind of where Kevlar and steel are now, in traditional armours or traditional kinds of body armour type protective equipment,” he says. “With this microscopic way of structuring nanotechnologies, you're essentially creating multiple shells, multiple layers, within the same space at a lighter weight. So, every time one of those layers meets resistance, it's providing extra protection.”
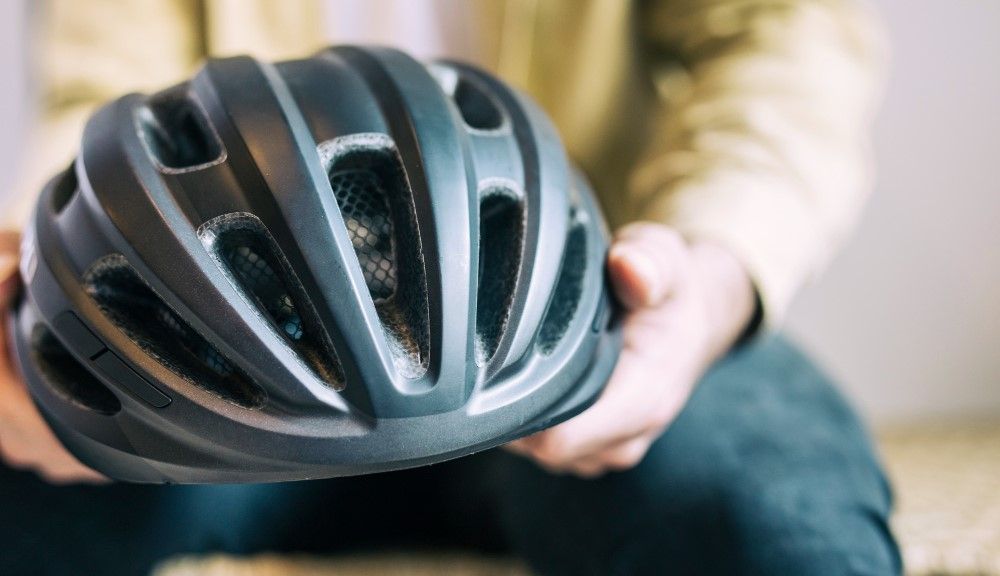
The key advantage is that nanotechnology is allowing for a multi-layered manufacture at the design stage - from the original concept.
This is in stark contrast to current composite technology used for body armour tends to focus on providing layers for which more and more protection can be added by adding more bulk. Kevlar composites, for example, are made of very stiff fibres which are either woven or arranged in certain patterns but are always basically a 2D layered pattern.
This newer technology makes use of what Portela calls ‘3D architecture’ which “gives rise to very interesting dissipation mechanisms,” such as tiny lattice structures which have exceptional strength but maintain an extremely low weight. A situation which he compares to a protective foam which is designed in its original form to be energy absorbent.
Of course, as with any innovative technology there is still much research to be done before Kevlar-style composites are removed from production.
“There are still a lot of open questions that need to be validated before we can say this is ready for direct application by troops,” acknowledges Portela. “For instance, one key hurdle is the scalability fabrication of these materials. So, we want to be able to fabricate these materials at square meter length scales eventually.”
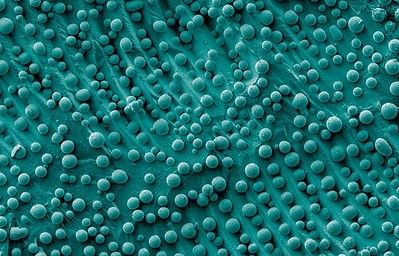
Despite these pressing questions, the advantages of using nanotechnology in future body armour design and manufacture are clear.
Nanotechnology allows for the customization of body armour to fit individual needs and preferences. By incorporating nanomaterials with specific properties, such as increased impact resistance or thermal conductivity, body armour can be tailored to provide optimal protection for different scenarios.
In addition, nanotechnology has enabled the development of self-healing materials for body armour. These materials have the ability to repair themselves when damaged, increasing the lifespan of the armour and reducing the need for frequent replacements.
Moreover, nanotechnology has improved the comfort and wearability of body armour. By reducing the weight and bulkiness of traditional armour raw materials, making it easier for soldiers, police officers, and bodyguards to move freely and comfortably.
From increased strength and durability to customization and self-healing capabilities, nanotechnology is transforming body armour. And as technology continues to advance, soldiers should expect even more innovations to provide extra safety in even the most dangerous situations.
All of which is happening thanks to nanotechnology.
You may also like to read: Developing an Exoskeleton: How Far Has Science Come? or Anti-Stab Vests with Nanotube Coating