Anti-Stab Vests with Nanotube Coating
A polyacrylate emulsion combines with nanotechnology for improved protective properties in combat gear, safety equipment, and packaging.
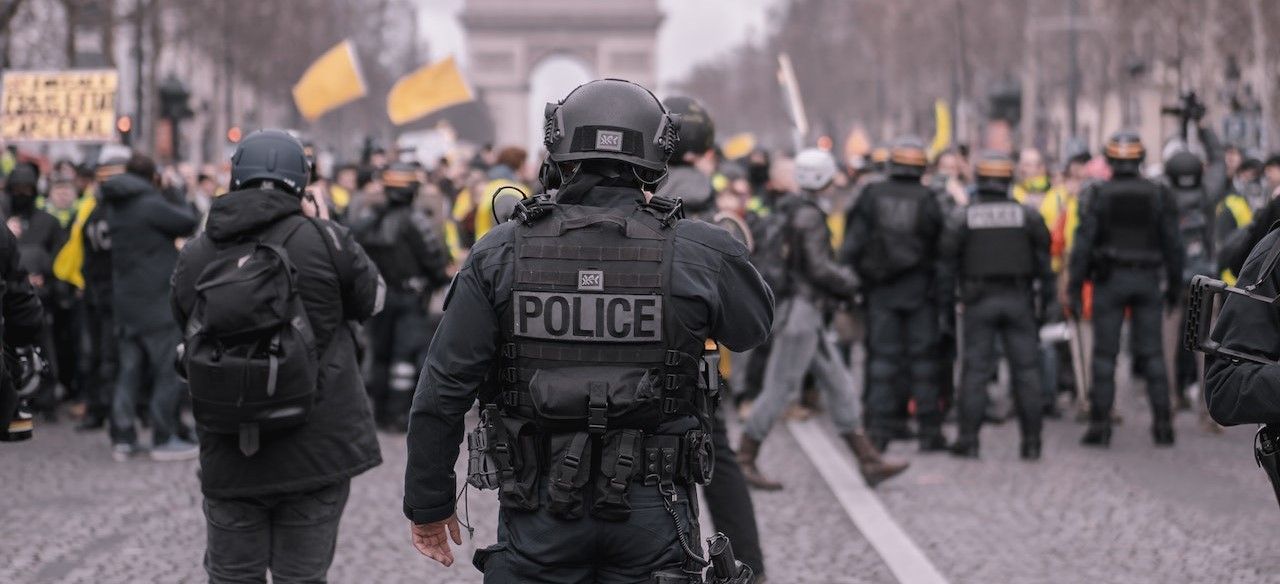
Anti-stab vests are now a standard piece of equipment in most police forces and security teams. However, current technology is far from perfect, such that a blade used with sufficient force can still penetrate them.
With global knife crime rising, the need to improve the shielding capabilities of materials used in the manufacture of personal body armour has increased. Nanomaterials and the skilled application of nanotechnology into raw materials already used in the production of protective vests may now solve this problem. All while maintaining ease of movement, low weight, flexibility, and comfort.
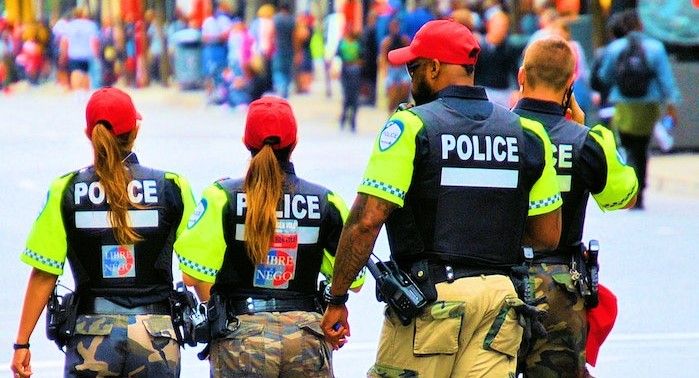
The most common raw material used to create soft body armour is aramid, ultra-high-molecular-weight polyethylene, or carbon and glass textiles.
They are used because the friction between yarn threads in these fabrics contribute to their puncture resistance. Up to a certain point, more friction equals more protection, so by making the fibre surfaces rougher, manufacturers can increase friction. However, the process is difficult and production output is low.
Alternatively, by including a different element, like a shear thickening fluid (STF) or a polyurethane (PU) coating, the bonding force between yarns can be strengthened. But these composite fabrics are unable to meet the demands for light weight, flexibility, and thinness at the same time.
To resolve this issue, a research team funded by the New Materials Research Key Program of Tianjin looked to employ the some of the strongest and toughest materials known to science – nanomaterials.
By applying a carbon nanotubes coating onto a polyacrylate emulsion that in turn was coated onto aramid fibres, researchers Ting-Ting Li, Xing-xiang Zhang, and their colleagues found remarkable improvements in stopping power and the ability of the textile to deflect energy away from the point of impact.
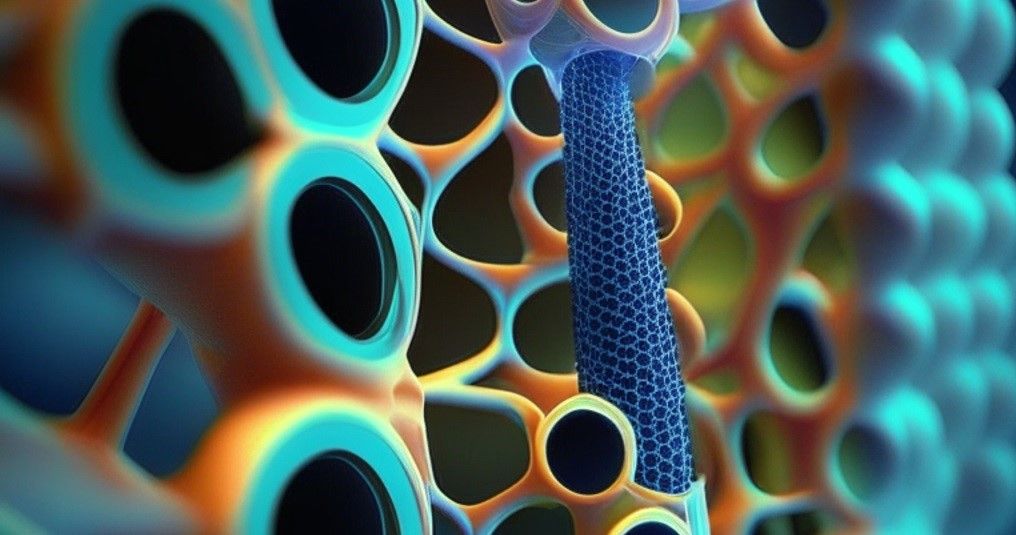
The study has now been published in the ACS journal Applied Nanomaterials, where the authors explain how, “A soft composite fabric was fabricated by coating a water-soluble polyacrylate emulsion (PAE) on the surface of aramid fabric (AF; AF/PAE). The areal weight of AF/PAE fabric was only 7.1% higher than that of AF ones.”
Tests conducted on the new material found significant improvement in defensive power. “Under spike stabbing, both the maximum load and energy absorption capacity of AF/PAE were about 4.5 times higher than those of AF. The puncture resistance of AF/PAE was superior to those of shear thickening fluid (STF)-impregnated AF (AF/STF) and polyurethane (PU)-sprayed AF (AF/PU) under the same areal weight or thickness.”
However, the addition of nanomaterials further improved the overall protection provided. The reports specifically stating that, “Carboxylic multi-walled carbon nanotubes (MWCNTs-COOH; 0.4 wt %) were then added to AF/PAE to further enhance the puncture resistance of the composite fabric. The spike punching resistance of AF/PAE increased by about 49.2% after the addition of MWCNTs-COOH. MWCNTs-COOH created a bridge effect between fibers to enhance friction between yarns.”
The nanomaterial coating also improved the dispersion of stress forces and reduced fibre fibrillation, further strengthening the material.
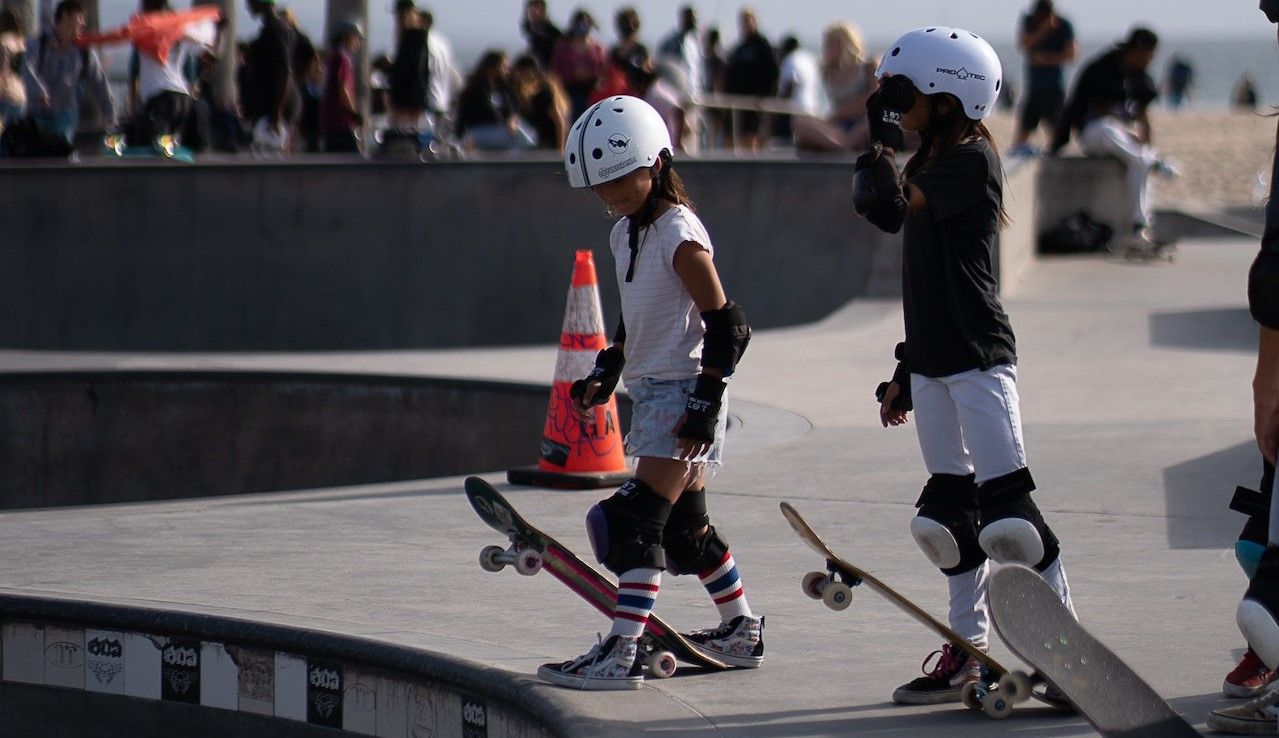
Such is the improved protection of the nanomaterial-enhanced fibres that it is envisaged that they could also be used in construction site safety gear, sturdy outdoor clothing, anti-slash clothing, military combat gear, helmets for both work and leisure usage, packaging materials, or general protective sports equipment such as shin guards or elbow pads.
Yet another case of how the smart application of nanotechnology can enhance raw materials and improve manufactured products.
If you would like to learn more about how nanomaterials can improve conventional raw materials you might like to read: Aramid Polymer Fibre Gains Electrical Conductivity from Nanotechor A Simple Nanotechnology for Modifying Industrial Polymers
Photo credit: Alotrobo on Pexels, Dave Romain, Daniel Torobekov, & Gencraft